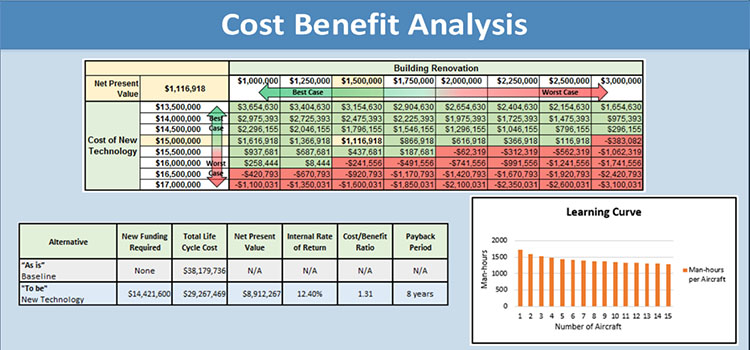
If you are undergoing a major change in your organization, you may be wondering why is change management important. Change management involves helping employees adapt to these changes. It includes providing them with the resources, capabilities and support they need during this period. It includes monitoring the effects of the change, making sure that employees feel safe and well-prepared, and communicating the new changes effectively. Change management can help improve employee performance if done correctly. There are many software tools that help you manage these changes, including mass communication and employee engagement.
Learn from the COVID-19 pandemic
In a pandemic situation, an effective response is critical to containing disease and minimizing the strain on health services. The virus can spread quickly through close contact and physical contact. Public health experts have made recommendations for people to wash their hands frequently and to avoid crowds, which could reduce the spread of the disease and the risk of infection. However, a lack of effective antivirals and immunomodulatory drugs means that a quick response is not feasible.
As the swine flu epidemic has revealed, a lack of universal health care leaves vulnerable populations susceptible. Even those who can afford medical care may be at risk of living in poverty. Good hygiene habits can reduce the economic burden and help to manage the disease curve. For example, people can avoid touching contaminated surfaces by washing their hands after using public restrooms or washing their face after coming in contact with an infected person.
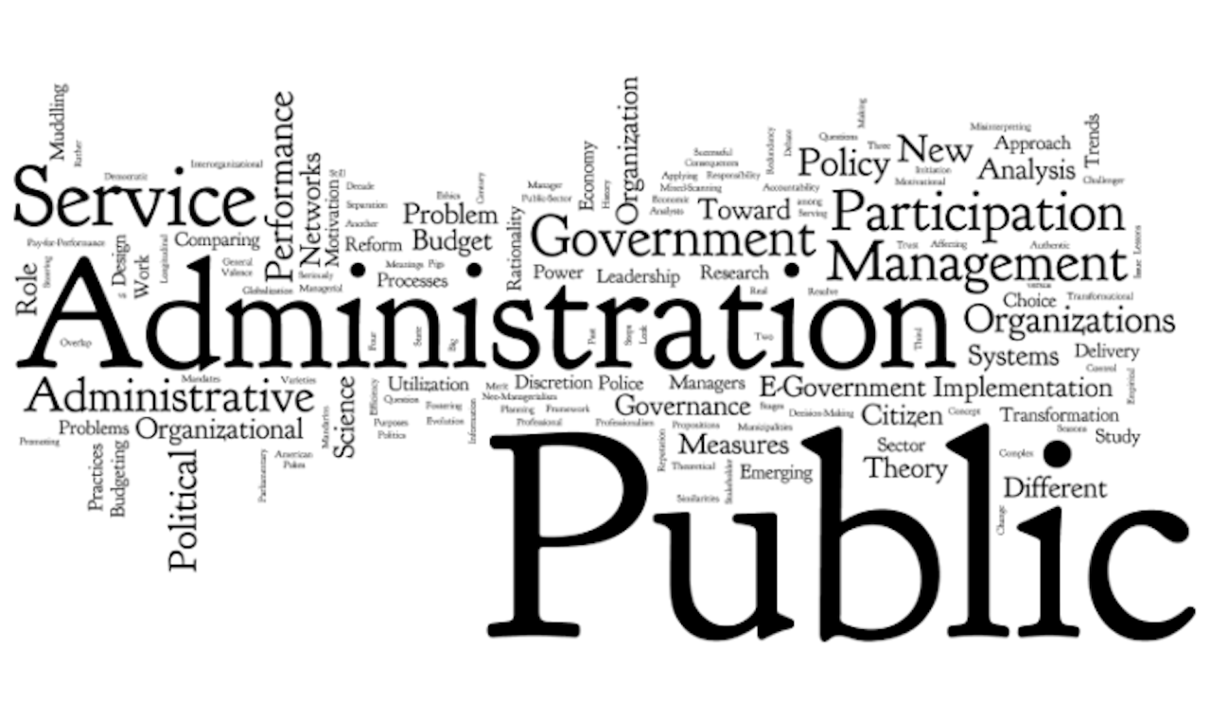
Benefits of Change Management
It can be hard to change business habits, but there are many benefits to managing change. It can make the whole organization more productive, and also improve efficiency. It improves morale, leading to fewer frustrations. Communication can be improved through change management, which can help you achieve your future goals and projects. It requires a lot of clarity and perspective to manage change. It requires collaboration among people from different departments.
Understanding why the change is occurring is critical during the process. To make change management successful, you must communicate why the change is taking place, what it is going on, and the expected results. Employees will be more inclined to support the change if they are clear about the purpose and the implementation methods. Clear communication channels should be maintained throughout the entire process to avoid miscommunications or misunderstandings.
Communication
Communication is essential to the success of change management. It can help employees understand and accept changes. It is important to communicate changes clearly and concisely with everyone involved in a new initiative. Employees should also be informed about the benefits of the changes. A change management workshop, for example, could be a good way to communicate information and discuss benefits of the new strategy. Training sessions could also be useful to learn new behaviors and ideas. Interactive tools such video content are a great way to communicate your changes to employees. Digital signage is another interactive tool that can help you communicate ideas to employees.
Managers must inform employees of the new strategy in order for them to effectively communicate the advantages of the change. Managers must inform their staff about the new strategy and project. This includes communicating all the benefits and drawbacks to the relevant parties. Employees should be kept informed about the change in a timely manner so that they can prepare for it. They should also be given enough time to ask any questions and offer their input. In order to overcome resistance, communication is essential. As a manager, it is important to anticipate resistance from your staff and be ready to respond.
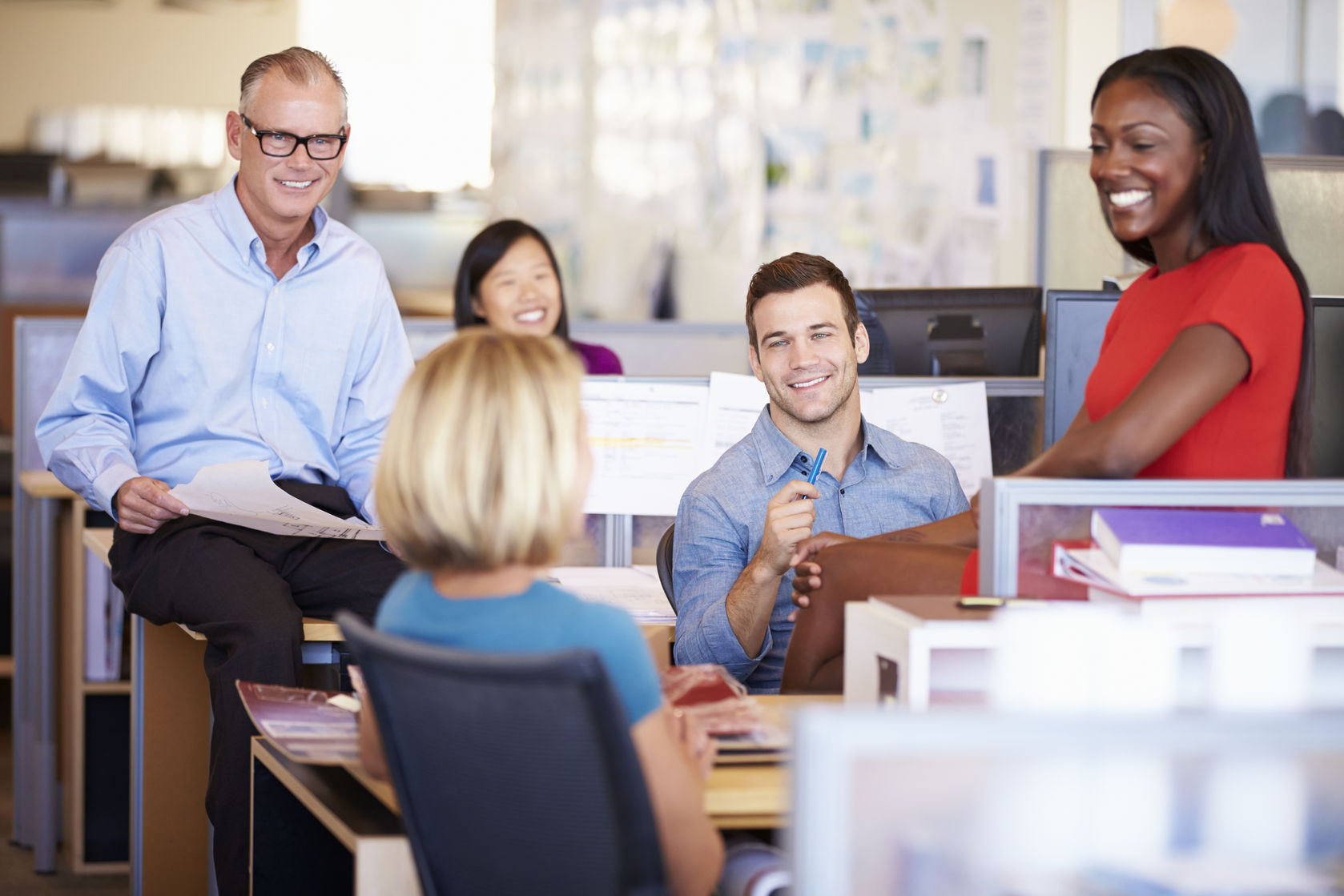
Minimizing risk
Risk is a major concern for any organization. It can cause financial losses or even the closure of a company. It can disrupt business processes. For example, companies that do not take risks and get disrupted by born-digital powerhouses could suffer a serious setback. The following guide explores key concepts, tools, and trends related to risk management. You will also find hyperlinks to further information.
One initiative is the most common way to implement change management. This approach is fine in sequential environments, but dynamic markets and new technologies have made it difficult for organizations to change faster than ever. Managers of change must be skilled in minimizing risk. However, many change managers lack the skills or experience necessary to achieve this goal. They must learn to identify and manage risks, as well as develop the right tools for their projects.
FAQ
What is the meaning of "project management?"
Management is the act of managing activities in order to complete a project.
This includes defining the scope, identifying the requirements and preparing the budget. We also organize the project team, schedule the work, monitor progress, evaluate results, and close the project.
How do we create a company culture that is productive?
A positive company culture creates a sense of belonging and respect in its people.
It is founded on three basic principles:
-
Everybody has something of value to share
-
People are treated fairly
-
Respect is shared between individuals and groups
These values are reflected in the way people behave. They will treat others with kindness and consideration.
They will listen to other people's opinions respectfully.
They can also be a source of inspiration for others.
In addition, the company culture encourages open communication and collaboration.
People feel free to express their views openly without fear of reprisal.
They know mistakes will be accepted as long as they are dealt with honestly.
Finally, the company culture encourages honesty as well as integrity.
Everyone is aware that truth must be told.
Everyone understands that there are rules and regulations which apply to them.
No one is entitled to any special treatment or favors.
What is the difference of a program and project?
A program is permanent while a project can be temporary.
A project typically has a defined goal and deadline.
It is usually done by a group that reports back to another person.
A program often has a set goals and objectives.
It is often implemented by one person.
What is Six Sigma?
It's a strategy for quality improvement that emphasizes customer care and continuous learning. The goal is to eradicate defects through statistical techniques.
Motorola's 1986 efforts to improve manufacturing process efficiency led to the creation of Six Sigma.
The idea spread quickly in the industry. Today many organizations use six-sigma techniques to improve product design.
How to manage employees effectively?
The key to effective management of employees is ensuring their happiness and productivity.
It also means having clear expectations of their behavior and keeping track of their performance.
Managers must be clear about their goals and those of their teams in order to succeed.
They must communicate clearly with their staff. They must communicate clearly with staff members.
They also need to keep records of their team's activities. These include:
-
What was accomplished?
-
How much work did you put in?
-
Who did it and why?
-
What was the moment it was completed?
-
Why was this done?
This information can be used to monitor performance and evaluate results.
What is the difference of leadership and management?
Leadership is about influence. Management is about controlling others.
A leader inspires followers while a manager directs workers.
A leader inspires others to succeed, while a manager helps workers stay on task.
A leader develops people; a manager manages people.
What's the difference between Six Sigma and TQM?
The main difference between these two quality management tools is that six sigma focuses on eliminating defects while total quality management (TQM) focuses on improving processes and reducing costs.
Six Sigma is an approach for continuous improvement. This approach emphasizes eliminating defects through statistical methods like control charts, Pareto analysis, and p-charts.
This method has the goal to reduce variation of product output. This is done by identifying and correcting the root causes of problems.
Total quality management is the measurement and monitoring of all aspects within an organization. It also involves training employees to improve performance.
It is often used to increase productivity.
Statistics
- This field is expected to grow about 7% by 2028, a bit faster than the national average for job growth. (wgu.edu)
- Our program is 100% engineered for your success. (online.uc.edu)
- As of 2020, personal bankers or tellers make an average of $32,620 per year, according to the BLS. (wgu.edu)
- 100% of the courses are offered online, and no campus visits are required — a big time-saver for you. (online.uc.edu)
- The average salary for financial advisors in 2021 is around $60,000 per year, with the top 10% of the profession making more than $111,000 per year. (wgu.edu)
External Links
How To
How is Lean Manufacturing done?
Lean Manufacturing methods are used to reduce waste through structured processes. They were developed by Toyota Motor Corporation in Japan during the 1980s. The primary goal was to make products with lower costs and maintain high quality. Lean manufacturing seeks to eliminate unnecessary steps and activities in the production process. It includes five main elements: pull systems (continuous improvement), continuous improvement (just-in-time), kaizen (5S), and continuous change (continuous changes). Pull systems are able to produce exactly what the customer requires without extra work. Continuous improvement refers to continuously improving existing processes. Just-intime refers the time components and materials arrive at the exact place where they are needed. Kaizen means continuous improvement. Kaizen involves making small changes and improving continuously. The 5S acronym stands for sort in order, shine standardize and maintain. These five elements are combined to give you the best possible results.
Lean Production System
The lean production system is based on six key concepts:
-
Flow - focuses on moving information and materials as close to customers as possible.
-
Value stream mapping - Break down each stage in a process into distinct tasks and create an overview of the whole process.
-
Five S's – Sort, Put In Order Shine, Standardize and Sustain
-
Kanban - visual cues such as stickers or colored tape can be used to track inventory.
-
Theory of constraints - identify bottlenecks during the process and eliminate them with lean tools like Kanban boards.
-
Just-in Time - Send components and material directly to the point-of-use;
-
Continuous improvement - incremental improvements are made to the process, not a complete overhaul.