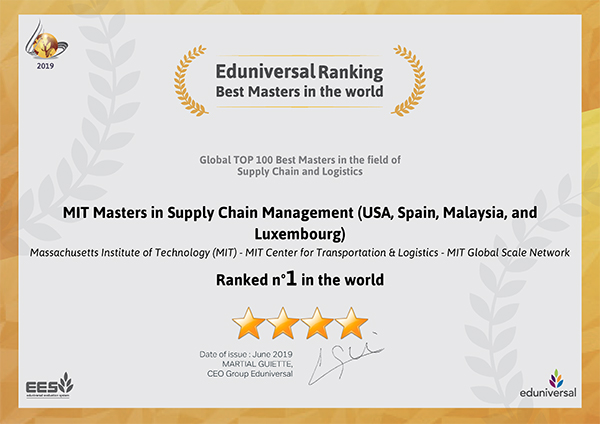
Forecasting based ANN
Artificial neural networks (ANNs), a widely-used tool in forecasting are often used by businesses. Various techniques have been developed to make ANNs more accurate. A new study aims to apply ANNs for Supply Chain Management. This research compares the performance between four different ANN types: the FSANN FWANN, HYANN and HYANN. HYANN is a combination FWANN/FSANN. It includes feature selection and weighting to improve performance.
Neural networks consist of many layers interconnected. Each layer is made up of a number neurons. The input layer is responsible for receiving external data and the output layer provides results. The hidden layer also contains neurons, which are used to refine results. Although the number of neurons in the input and output layers are fixed, the number of neurons in the hidden layer can vary. It depends on how many layers are hidden, whether there are bias neurons or not, and what the learning rate is.
Probabilistic forecasting
Probabilistic prediction can be applied in many areas of supply chain management. Its main focus is to reduce uncertainty in making decisions. It is crucial to take into account all sources of uncertainty, even those that may not be easily quantifiable. This approach can be used to help companies plan their inventory.
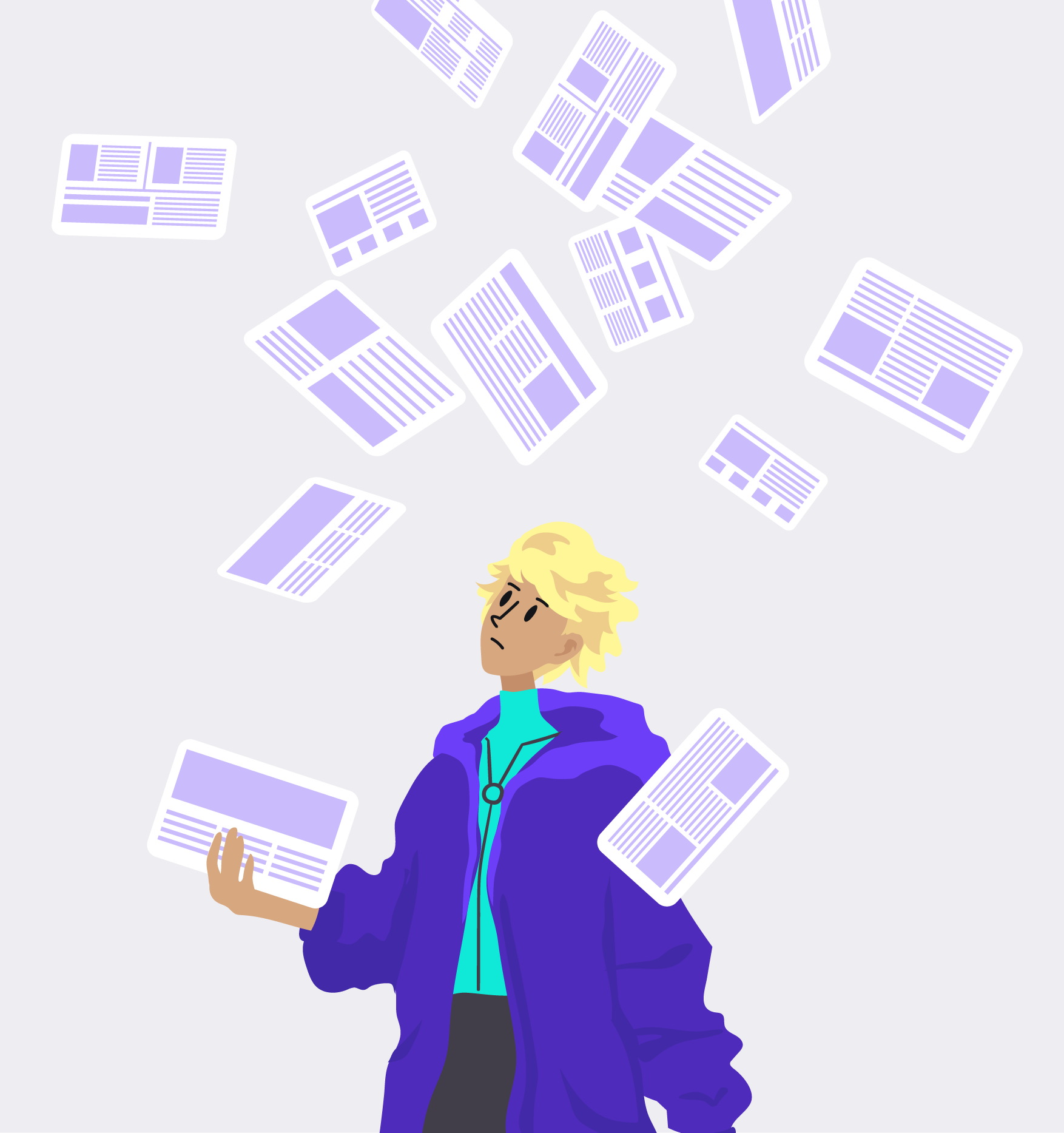
A probabilistic forecast involves creating different scenarios for different outcomes. It may include uncertainties like uncertain demand, uncertain lead time, and unanticipated return from customers. You can also think about the uncertainty surrounding when an order will arrive from a supplier. It is possible to assess the uncertainty involved in these scenarios manually by having a detailed understanding of the context.
Regression analysis
Forecasting supply chain management may be hard. However, regression analysis could help. It forces businesses to analyze actual data. If a company wants to know the rainy season, they can plot sales versus rainfall for the past three years. This will show them the peak sales.
Forecasting demand for a specific product requires a statistical model that is based upon past data. The model is then refined with current data, and tested against historical data. Only then can the forecasting tool be used for future trends. Supply chain managers need to be aware of the limitations of supply chain forecasting models.
AI
AI is a disruptive technology that can help supply chain managers anticipate future needs, and it can also reduce processing time. AI also allows for smarter decision-making. It provides valuable insights into market trends, weather patterns, and other variables. These data can have a significant impact on customer relations and industry credibility. It can help companies determine where and why bottlenecks occur.

AI forecasting may be able to help improve supply chain management. It can also improve the forecasting process through analysis of historical data, current trends, and social media chatter. AI can be used to help logistic operators predict demand and make it clear throughout the supply chain.
FAQ
What is the difference between management and leadership?
Leadership is all about influencing others. Management is about controlling others.
A leader inspires followers while a manager directs workers.
A leader motivates people and keeps them on task.
A leader develops people; a manager manages people.
What are the four major functions of Management?
Management is responsible of planning, organizing, leading, and controlling people as well as resources. It also includes developing policies and procedures and setting goals.
Management is the ability to direct, coordinate, control, motivate, supervise, train, and evaluate an organization's efforts towards achieving its goals.
Management has four primary functions:
Planning – Planning involves deciding what needs to happen.
Organizing is the act of deciding how things should go.
Directing - This refers to getting people follow instructions.
Controlling – Controlling is the process of ensuring that tasks are completed according to plan.
What are the 5 management processes?
Each business has five stages: planning, execution and monitoring.
Planning means setting goals for the long-term. This includes setting goals for the future and defining what you want.
Execution takes place when you actually implement the plans. These plans must be adhered to by everyone.
Monitoring allows you to monitor your progress towards achieving your goals. Monitoring should include regular reviews of performance against goals and budgets.
Review events take place at each year's end. They give you an opportunity to review the year and assess how it went. If not, then it may be possible to make adjustments in order to improve performance next time.
Evaluation takes place after the annual review. It helps identify what worked well and what didn't. It also provides feedback on the performance of people.
What are the 3 basic management styles?
The three basic management styles are: authoritarian, laissez-faire, and participative. Each style has its own strengths and weaknesses. Which style do you prefer? Why?
Autoritarian - The leader sets direction and expects everyone else to follow it. This style works best in large organizations that are stable and well-organized.
Laissez-faire is a leader who allows everyone to make their own decisions. This style works best when the organization is small and dynamic.
Participative: The leader listens to everyone's ideas and suggestions. This style is best for small organizations where everyone feels valued.
How do you manage your employees effectively?
Managing employees effectively means ensuring that they are happy and productive.
It also means having clear expectations of their behavior and keeping track of their performance.
To do this successfully, managers need to set clear goals for themselves and for their teams.
They need to communicate clearly and openly with staff members. And they need to ensure that they reward good performance and discipline poor performers.
They should also keep records of all activities within their team. These include:
-
What did we accomplish?
-
What was the work involved?
-
Who did it?
-
It was done!
-
Why?
This data can be used to evaluate and monitor performance.
What role should a manager play within a company
Different industries have different roles for managers.
The manager oversees the day-to-day activities of a company.
He/she ensures that the company meets its financial obligations and produces goods or services that customers want.
He/she ensures that employees follow the rules and regulations and adhere to quality standards.
He/she oversees marketing campaigns and plans new products.
What are the steps of the management decision-making process?
Managers have to make complex decisions. It involves many factors, such as analysis and strategy, planning, execution, measurement, evaluation, feedback etc.
The key thing to remember when managing people is that they are human beings just as you are and therefore make mistakes. As such, there is always room for improvement, especially if you're willing to put forth the effort to improve yourself first.
We explain in this video how the Management decision-making process works. We will discuss the various types of decisions, and why they are so important. Every manager should be able to make them. The following topics will be covered.
Statistics
- Your choice in Step 5 may very likely be the same or similar to the alternative you placed at the top of your list at the end of Step 4. (umassd.edu)
- Hire the top business lawyers and save up to 60% on legal fees (upcounsel.com)
- 100% of the courses are offered online, and no campus visits are required — a big time-saver for you. (online.uc.edu)
- This field is expected to grow about 7% by 2028, a bit faster than the national average for job growth. (wgu.edu)
- UpCounsel accepts only the top 5 percent of lawyers on its site. (upcounsel.com)
External Links
How To
How do I do the Kaizen Method?
Kaizen means continuous improvement. The term was coined in the 1950s at Toyota Motor Corporation and refers to the Japanese philosophy emphasizing constant improvement through small incremental changes. It's a team effort to continuously improve processes.
Kaizen, a Lean Manufacturing method, is one of its most powerful. This concept requires employees to identify and solve problems during manufacturing before they become major issues. This way, the quality of products increases, and the cost decreases.
Kaizen is an approach to making every worker aware and alert to what is happening around them. Correct any errors immediately to avoid future problems. Report any problem you see at work to your manager.
Kaizen follows a set of principles. We always start from the end product and move toward the beginning. We can improve the factory by first fixing the machines that make it. Next, we repair the machines that make components. Then, the machines that make raw materials. We then fix the workers that work with those machines.
This method, called 'kaizen', focuses on improving each and every step of the process. Once we have finished fixing the factory, we return to the beginning and work until perfection.
Before you can implement kaizen into your business, it is necessary to learn how to measure its effectiveness. There are several ways to determine whether kaizen is working well. One way is to examine the amount of defects on the final products. Another method is to determine how much productivity has improved since the implementation of kaizen.
To determine if kaizen is effective, you should ask yourself why you chose to implement kaizen. You were trying to save money or obey the law? Did you really believe that it would be a success factor?
If you answered yes to any one of these questions, congratulations! You are ready to start kaizen.