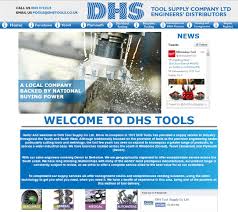
A certified construction manager is a qualified professional in the field of construction. These professionals must pass an examination to prove their skills. The exam is practical and measures the knowledge of the candidate in the field of construction. The duration of the examination depends on the qualification. The average passing time is four hours.
Earnings potential
A degree as a manager of construction can make you a very lucrative candidate. While the average education is four years, you can earn a master's of construction management in just one year. A year of work experience will be required before you can begin your pursuit of certification.
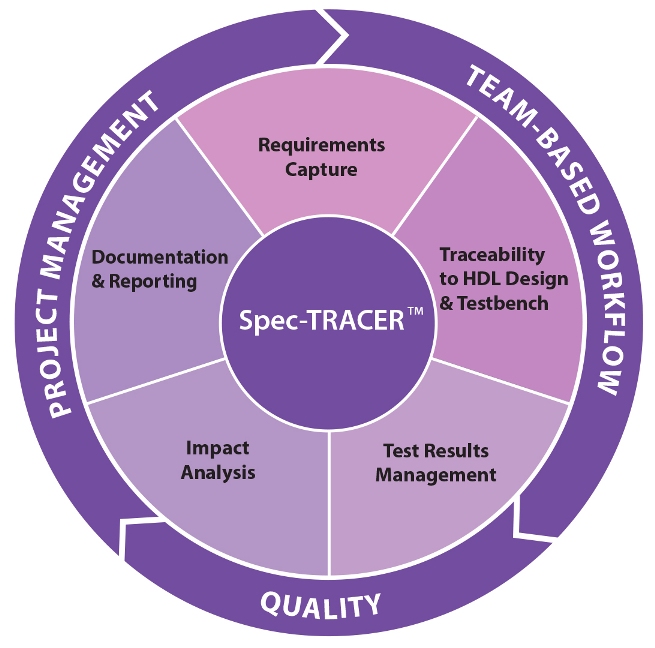
Earning a certificate for construction management can help increase your earnings potential and keep your licenses and certifications current. A certification course can help you keep up to date on safety and compliance.
Credentials required
Certification is a great way to increase your skills, whether you are looking to build a career as a construction manager or just to improve your resume. Certification can validate your knowledge and dedication to the field. It can also help you get the job of your dreams faster. There are many certifications to choose from. Make sure you find the one that is right for your career.
First, you will need to pass a six-hour exam consisting of 200 questions. The test is a practical assessment that tests your knowledge of safety and construction management. Once you pass the test, you can get access to a mentor directory and become a Certified Construction Manager. After earning the credential you can keep it for up seven years. However, the exam must be taken again every seven year.
Job duties
A construction manager is an individual with special knowledge in building construction. They work closely together with civil engineers, and other building specialists to complete projects. They negotiate and manage construction contracts. They are responsible for selecting contractors and subcontractors. They may have to interact with lawyers or officials from the local government.
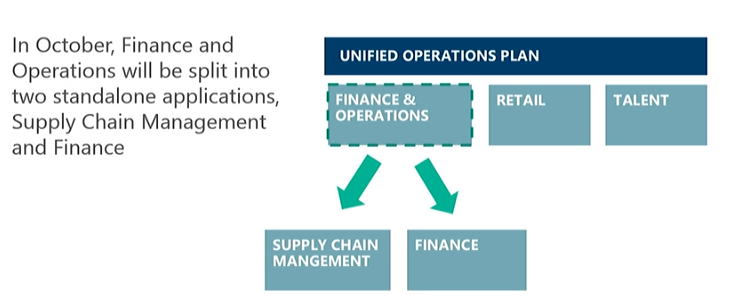
Construction managers must be able to identify and mitigate risks to ensure a successful project. A construction manager must also be able to work well with multiple teams in order to ensure that every aspect of the construction process is being done to the highest standard. This position typically requires a bachelor's in construction management and at least five years of relevant work experience. A construction manager must also have exceptional communication skills to manage multiple audiences and address issues and disputes.
FAQ
What are the steps that management takes to reach a decision?
The decision-making process for managers is complex and multifaceted. It includes many factors such as analysis, strategy planning, implementation and measurement. Evaluation, feedback and feedback are just some of the other factors.
When managing people, the most important thing to remember is that they are just human beings like you and make mistakes. You can always improve your performance, provided you are willing to make the effort.
We explain in this video how the Management decision-making process works. We discuss the different types of decisions and why they are important, every manager should know how to navigate them. These topics are covered in this course:
It can sometimes seem difficult to make business decisions.
Complex business systems have many moving parts. It is difficult for people in charge of businesses to manage multiple priorities simultaneously and also deal with uncertainty.
Understanding how these factors impact the whole system is key to making informed decisions.
It is important to consider the functions and reasons for each part of the system. You then need to consider how those individual pieces interact with each other.
You need to ask yourself if your previous actions have led you to make unfounded assumptions. If not, you might want to revisit them.
You can always ask someone for help if you still have questions after all of this. You may be able to see things from a different perspective than you are and gain insight that can help you find a solution.
How do you manage employees effectively?
Effectively managing employees means making sure they are productive and happy.
It also means having clear expectations of their behavior and keeping track of their performance.
To do this successfully, managers need to set clear goals for themselves and for their teams.
They should communicate clearly with employees. They need to communicate clearly with their staff.
They also need to keep records of their team's activities. These include:
-
What was achieved?
-
How much work were you able to accomplish?
-
Who did it all?
-
When it was done?
-
Why did it happen?
This information can be used to monitor performance and evaluate results.
How can a manager enhance his/her leadership skills?
It is important to have good management skills.
Managers need to monitor their subordinates' performance.
You must act quickly if you notice that your subordinate isn’t performing to their standards.
You should be able to identify what needs improvement and how to improve things.
What are management concepts?
Management concepts are the principles and practices used by managers to manage people, resources. These include topics such as human resource policies and job descriptions, performance assessments, training programs and employee motivation.
What is Six Sigma?
It's a method for quality improvement that focuses on customer service as well as continuous learning. The objective is to eliminate all defects through statistical methods.
Six Sigma was developed at Motorola in 1986 as part of its efforts to improve manufacturing processes.
The idea spread quickly throughout the industry, and today, many organizations are using six sigma methods to improve product design, production, delivery, and customer service.
What kind people use Six Sigma?
Six Sigma will most likely be familiar to people who have worked in statistics and operations research. However, anyone involved in any aspect of business can benefit from using it.
Because it requires a high level of commitment, only those with strong leadership skills will make an effort necessary to implement it successfully.
Statistics
- The average salary for financial advisors in 2021 is around $60,000 per year, with the top 10% of the profession making more than $111,000 per year. (wgu.edu)
- 100% of the courses are offered online, and no campus visits are required — a big time-saver for you. (online.uc.edu)
- UpCounsel accepts only the top 5 percent of lawyers on its site. (upcounsel.com)
- Our program is 100% engineered for your success. (online.uc.edu)
- The profession is expected to grow 7% by 2028, a bit faster than the national average. (wgu.edu)
External Links
How To
How do I do the Kaizen Method?
Kaizen means continuous improvement. The term was coined in the 1950s at Toyota Motor Corporation and refers to the Japanese philosophy emphasizing constant improvement through small incremental changes. This is a collaborative process in which people work together to improve their processes continually.
Kaizen is one method that Lean Manufacturing uses to its greatest advantage. In this concept, employees who are responsible for the production line must identify problems that exist during the manufacturing process and try to solve them before they become big issues. This way, the quality of products increases, and the cost decreases.
Kaizen is a way to raise awareness about what's happening around you. Correct any errors immediately to avoid future problems. Report any problem you see at work to your manager.
Kaizen is based on a few principles. Start with the end product, and then move to the beginning. We can improve the factory by first fixing the machines that make it. We then fix the machines producing components, and the machines producing raw materials. And finally, we fix the workers who work directly with those machines.
This approach is called 'kaizen' because it focuses on improving everything steps by step. When we are done fixing the whole factory, we go back to the beginning and continue until we reach perfection.
Before you can implement kaizen into your business, it is necessary to learn how to measure its effectiveness. There are several ways to determine whether kaizen is working well. Another way to determine if kaizen is working well is to look at the quality of the products. Another way to find out how productive your company has been since you implemented kaizen is to measure the increase in productivity.
You can also find out if kaizen works by asking yourself why you decided to implement it. Is it because the law required it or because you want to save money. You really believed it would make you successful?
If you answered yes to any one of these questions, congratulations! You are ready to start kaizen.