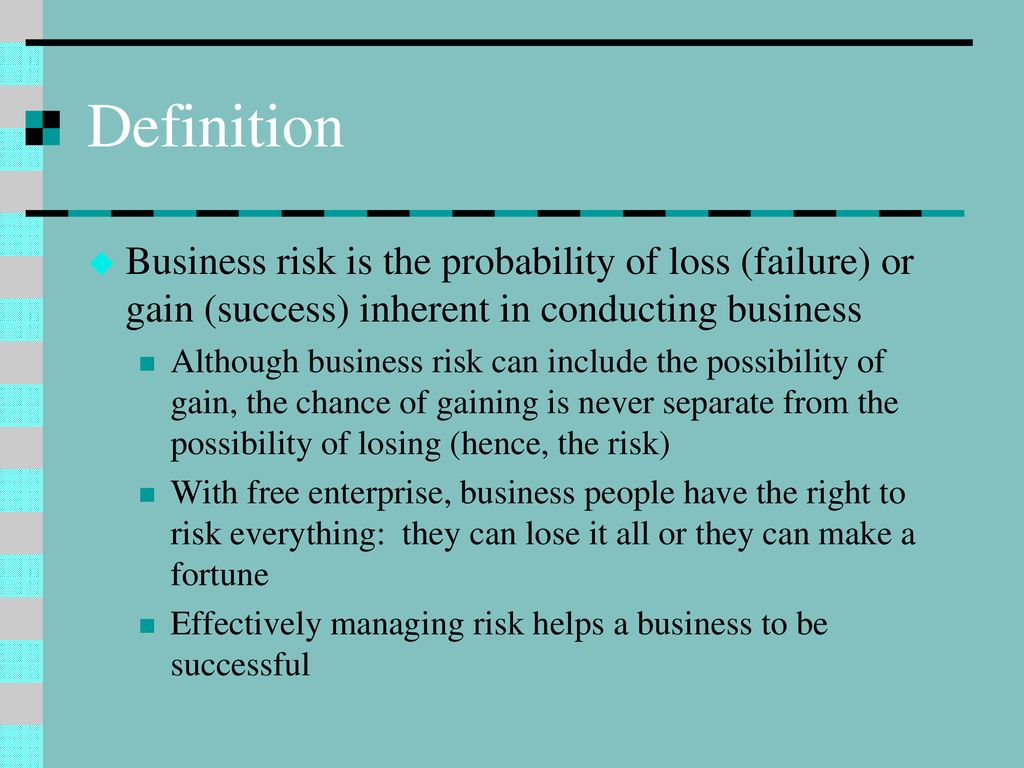
Compliance jobs may interest you if your background is in finance, law, and other related industries. These entry-level jobs provide valuable experience and expose you to compliance regulations. Although professional certifications do not need to be obtained, employers will prefer candidates with credentials. Certifications often require courses and ongoing continuing education credits. Certifications are valuable tools to keep your compliance skills up-to date.
Experience in a related industry
If you're looking to land a compliance job, it's crucial to have some relevant experience. If you are a paralegal, for example, you might gain valuable insight working in the backoffice of a law company. Experience in a related industry is also a good starting point.
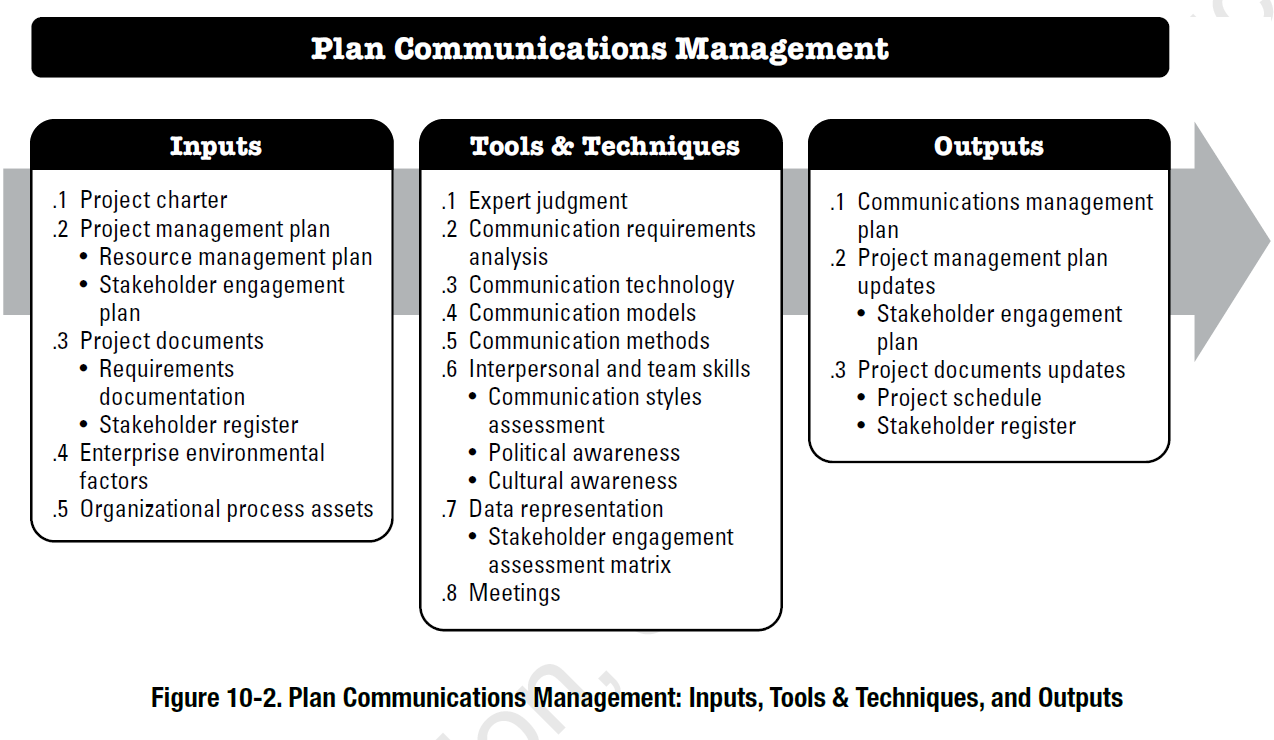
Along with the required compliance skills, leadership experience is a must. To be successful in a job as a compliance officer, you need to be able manage a team, take initiative, and communicate effectively and efficiently with both internal and externe stakeholders. You should also have excellent oral, quantitative, as well as analytical communication skills.
Salary
There are a number of factors that go into determining the salary for a compliance job. The salary of a compliance manager is determined by experience, education, and geographic location. Robert Half, a major salary research firm, estimates a compliance chief earning $209,000 by 2022. It is 1.5% more than the previous year.
Most of the highest-paid compliance jobs are in banks, hedge funds, or other large businesses. They typically have a competitive salary and high potential for bonuses. With benefits like share options or out-of-office flexibility, compliance jobs at fintech businesses are becoming more attractive.
Responsibilities
You can have many different responsibilities when it comes to compliance. No matter the role, compliance managers need to be familiar with legal and regulatory issues. This includes advising employees and their managers. They can also help to identify potential violations and conduct investigations.
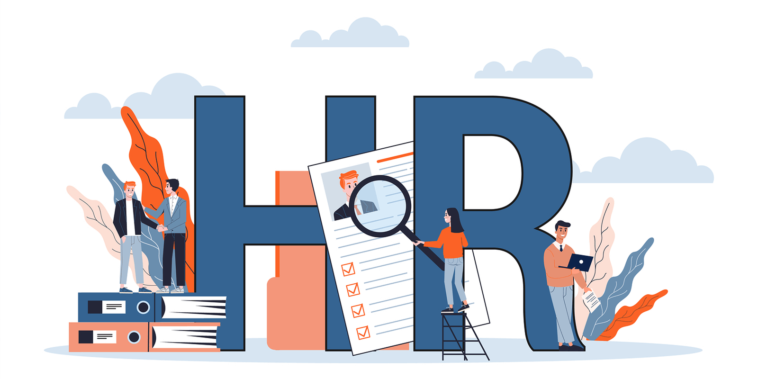
Compliance professionals can move quickly up the career ladder. They can easily go from junior compliance officer to senior officer in two to four years. They may eventually move up to senior management or compliance managers, which requires at least five years' experience. A linear progression is common in compliance jobs within large corporate companies. In a large firm, an analyst may progress to an associate vice president, then a vice president. An analyst may move up to the rank of associate vice president in a large firm, and then to the rank of vice president.
FAQ
What does the term "project management” mean?
We mean managing the activities involved in carrying out a project.
These include planning the scope and identifying the needs, creating the budget, organizing the team, scheduling the work and monitoring progress. Finally, we close down the project.
It can sometimes seem difficult to make business decisions.
Complex systems and many moving parts make up businesses. Their leaders must manage multiple priorities, as well as dealing with uncertainty.
It is important to understand the effects of these factors on the system in order to make informed decisions.
You need to be clear about the roles and responsibilities of each system. Then, you need to think about how these pieces interact with one another.
Ask yourself if there are hidden assumptions that have influenced your behavior. If you don't have any, it may be time to revisit them.
Asking for assistance from someone else is a good idea if you are still having trouble. They may see things differently from you and have insights that could help you find a solution.
What are your main management skills
Management skills are essential for any business owner, whether they're running a small local store or an international corporation. They include the ability to manage people, finances, resources, time, and space, as well as other factors.
You will need management skills to set goals and objectives, plan strategies, motivate employees, resolve problems, create policies and procedures, and manage change.
You can see that there are many managerial duties.
How do you define Six Sigma?
Six Sigma is well-known to those who have worked in operations research and statistics. Anybody involved in any aspect or business can benefit.
Because it requires a high degree of commitment, only leaders with strong leadership skills can implement it successfully.
How can a manager motivate his/her staff?
Motivation refers to the desire to perform well.
Doing something that is enjoyable can help you get motivated.
Or you can get motivated by seeing yourself making a contribution to the success of the organization.
For example, if you want to become a doctor, you'll probably find it more motivating to see patients than to study medicine books all day.
The inner motivation is another type.
One example is a strong sense that you are responsible for helping others.
You may even find it enjoyable to work hard.
If you feel unmotivated, ask yourself why.
Then think about how you can make your life more motivating.
Statistics
- Our program is 100% engineered for your success. (online.uc.edu)
- Hire the top business lawyers and save up to 60% on legal fees (upcounsel.com)
- Your choice in Step 5 may very likely be the same or similar to the alternative you placed at the top of your list at the end of Step 4. (umassd.edu)
- 100% of the courses are offered online, and no campus visits are required — a big time-saver for you. (online.uc.edu)
- The profession is expected to grow 7% by 2028, a bit faster than the national average. (wgu.edu)
External Links
How To
How does Lean Manufacturing work?
Lean Manufacturing uses structured methods to reduce waste, increase efficiency and reduce waste. They were created by Toyota Motor Corporation in Japan in the 1980s. The main goal was to produce products at lower costs while maintaining quality. Lean manufacturing seeks to eliminate unnecessary steps and activities in the production process. It includes five main elements: pull systems (continuous improvement), continuous improvement (just-in-time), kaizen (5S), and continuous change (continuous changes). Pull systems are able to produce exactly what the customer requires without extra work. Continuous improvement involves constantly improving upon existing processes. Just-in time refers to components and materials being delivered right at the place they are needed. Kaizen stands for continuous improvement. Kaizen can be described as a process of making small improvements continuously. Fifth, the 5S stand for sort, set up in order to shine, standardize, maintain, and standardize. To achieve the best results, these five elements must be used together.
Lean Production System
Six key concepts form the foundation of the lean production system:
-
Flow - focus on moving material and information as close to customers as possible;
-
Value stream mapping - break down each stage of a process into discrete tasks and create a flowchart of the entire process;
-
Five S's: Sort, Shine Standardize, Sustain, Set In Order, Shine and Shine
-
Kanban is a visual system that uses visual cues like stickers, colored tape or stickers to keep track and monitor inventory.
-
Theory of Constraints - Identify bottlenecks in the process, and eliminate them using lean tools such kanban boards.
-
Just-in Time - Send components and material directly to the point-of-use;
-
Continuous improvement - incremental improvements are made to the process, not a complete overhaul.