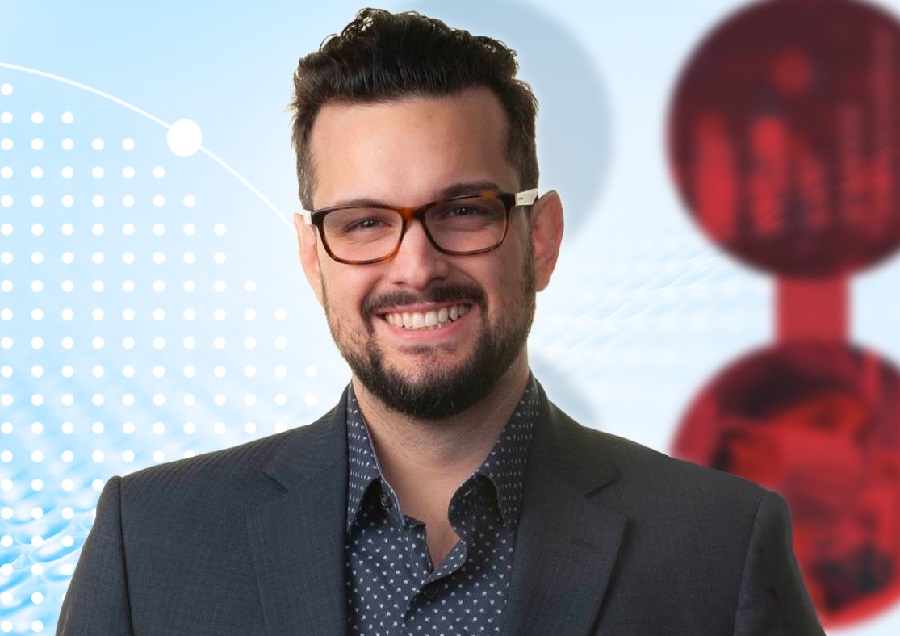
It is important to maintain consistency between contracts in construction projects that involve multiple parties. Many times, a prime contract contains provisions that can be extended to subcontractors as well. To ensure that all agreements are in accordance, it is crucial for all parties to a project to get a copy the prime contract.
Job order
Job order contracting (JOC), is a method for project management that reduces costs, time and errors. It can also be used to quickly respond to ongoing projects and clear any deferred maintenance. JOC is flexible and more flexible than other contracting models.
Through job order contracting, both the project owner as well as the contractor can be more transparent starting from day one. They know each other's background and work history and can trust each other. This also helps to reduce change orders. The owner and contractor will have a greater understanding of each others' work, which can help them to build a stronger partnership. This prevents miscommunications and errors from causing many changes.
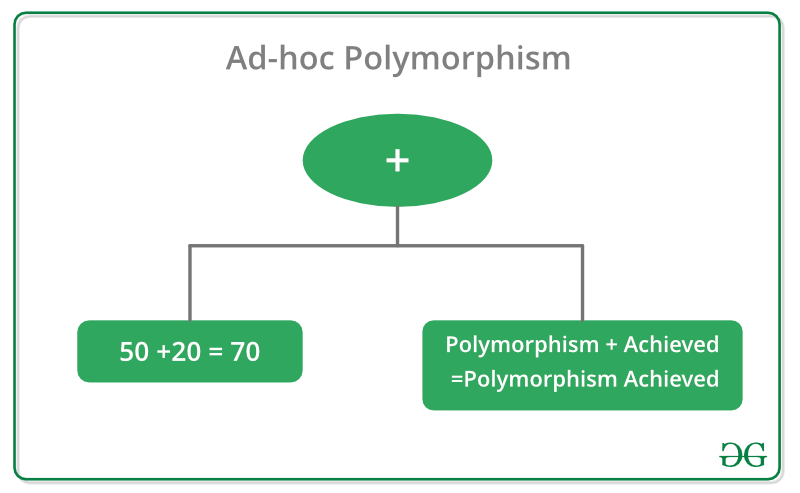
Incentive
Incentive contracting refers to a form collaboration between a contractor on a project and the client. The goal of incentivizing contracting is to maximise value for money. An incentive contract has two components: a target price and a share formula. The project's cost outturn should be accurately estimated and the target price is set through a competitive process. The contractor gets paid a fee that covers their overheads. The share formula introduces an incentive to the contract and determines how much should be divided between the parties.
Incentive contracts provide transparency and accountability. Contractors are more likely be to give owners timely updates when they are fully aware of the work in process. This encourages closer collaboration and more skill-based assignments.
Lump-sum
Lump-sum construction contracting is a method of contracting where a fixed amount is agreed upon at the beginning. This type of contract includes a fixed target and inputs as well as outputs. It is best used when the project is well-defined and requires little variation. There are disadvantages to lump sum contracting.
Lack of transparency is one of the disadvantages. Contractors can conceal their profit margins. Contractors are not required to present detailed costs estimates or invoices to the owner. A disadvantage of lump-sum agreements is that they are subject to disputes and claims due to unsatisfactory contractual terms. For instance, in some projects, the contractor may produce an unbalanced bid, in which unit prices are increased for items that are used later in the project. This can lead disputes over the payment rates.
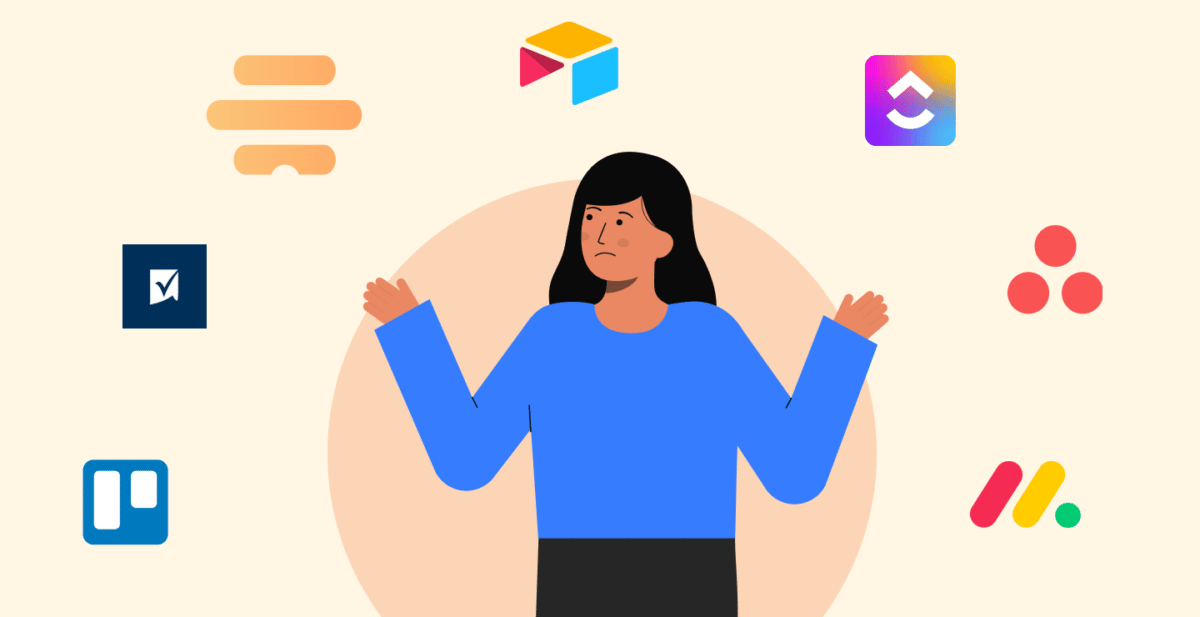
Delivery of integrated projects
Integrated Project Delivery, also known as IPD, is a new delivery method for construction projects. It eliminates obstacles that can hinder project performance and aligns stakeholders towards a common goal. It increases the likelihood that projects will succeed by doing this. Implementing IPD means a change in traditional project management techniques and increased planning. Some of the major barriers to IPD include legal concerns, mistrust among key parties, and a lack of owner willingness. Fortunately, many organizations and professional bodies involved in the built environment are becoming aware of the benefits of IPD and are starting to implement it in smaller projects.
IPD has the advantage of completing projects quicker and reducing costs. This method allows all parties to concentrate on their strengths, which leads to higher client satisfaction.
FAQ
Why does it sometimes seem so hard to make good business decisions
Complex business systems have many moving parts. It is difficult for people in charge of businesses to manage multiple priorities simultaneously and also deal with uncertainty.
The key to making good decisions is to understand how these factors affect the system as a whole.
It is important to consider the functions and reasons for each part of the system. Then, you need to think about how these pieces interact with one another.
Also, you should ask yourself if there have been any assumptions in your past behavior. If you don't have any, it may be time to revisit them.
Asking for assistance from someone else is a good idea if you are still having trouble. They might have different perspectives than you, and could offer insight that could help you solve your problem.
How does a manager motivate their employees?
Motivation is the desire for success.
Enjoyable activities can motivate you.
You can also get motivated by seeing your contribution to the success or the improvement of the organization.
For example, if your goal is to become a physician, you will probably find it more motivational to see patients rather than to read a lot of medicine books.
A different type of motivation comes directly from the inside.
Perhaps you have a strong sense to give back, for example.
Perhaps you enjoy working hard.
Ask yourself why you aren't feeling motivated.
You can then think of ways to improve your motivation.
What kind of people use Six Sigma
Six Sigma is well-known to those who have worked in operations research and statistics. However, anyone involved in any aspect of business can benefit from using it.
Because it requires a high degree of commitment, only leaders with strong leadership skills can implement it successfully.
Statistics
- Hire the top business lawyers and save up to 60% on legal fees (upcounsel.com)
- UpCounsel accepts only the top 5 percent of lawyers on its site. (upcounsel.com)
- 100% of the courses are offered online, and no campus visits are required — a big time-saver for you. (online.uc.edu)
- As of 2020, personal bankers or tellers make an average of $32,620 per year, according to the BLS. (wgu.edu)
- This field is expected to grow about 7% by 2028, a bit faster than the national average for job growth. (wgu.edu)
External Links
How To
How is Lean Manufacturing done?
Lean Manufacturing uses structured methods to reduce waste, increase efficiency and reduce waste. These processes were created by Toyota Motor Corporation, Japan in the 1980s. It was designed to produce high-quality products at lower prices while maintaining their quality. Lean manufacturing emphasizes removing unnecessary steps from the production process. It includes five main elements: pull systems (continuous improvement), continuous improvement (just-in-time), kaizen (5S), and continuous change (continuous changes). Pull systems allow customers to get exactly what they want without having to do extra work. Continuous improvement involves constantly improving upon existing processes. Just-in-time is when components and other materials are delivered at their destination in a timely manner. Kaizen is continuous improvement. This can be achieved by making small, incremental changes every day. Five-S stands for sort. It is also the acronym for shine, standardize (standardize), and sustain. These five elements are used together to ensure the best possible results.
Lean Production System
Six key concepts form the foundation of the lean production system:
-
Flow - The focus is on moving information and material as close as possible to customers.
-
Value stream mapping: This is a way to break down each stage into separate tasks and create a flowchart for the entire process.
-
Five S's – Sort, Put In Order Shine, Standardize and Sustain
-
Kanban: Use visual signals such stickers, colored tape, or any other visual cues, to keep track your inventory.
-
Theory of constraints: identify bottlenecks in your process and eliminate them using lean tools, such as kanban board.
-
Just-in-time - deliver components and materials directly to the point of use;
-
Continuous improvement - Make incremental improvements rather than overhauling the entire process.