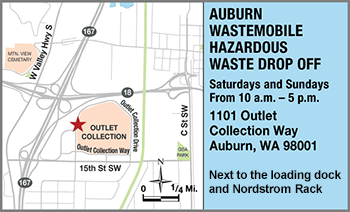
Asu offers an online Master's Degree in Sustainability Leadership and a Graduate Certificate on Sustainable Tourism. You can also earn concurrent degrees like an Executive Master in Sustainability Leadership. These programs can be completed in two years or less. You will need to fill out an application in order to get started.
For asu online sustainability, you will need to have concurrent degrees
Concurrent degrees, sometimes referred to by double majors, are those students who obtain two different degrees or diplomas simultaneously. Students have the option to choose from several degree programs. However there is a lot of overlap in curriculum. Students enrolled in concurrent degree programs must fulfill general university requirements as well as program admissions requirements. Applications with a minimum of 3.0 cumulative transfer grade are encouraged to apply. Candidates who fall below the limit will be reviewed on a case-by–case basis.
Students learn how to integrate economic, political, and social factors into engineering practice. This program emphasizes interdisciplinarity. Students develop technical and ethical skills to address sustainability issues and create solutions.
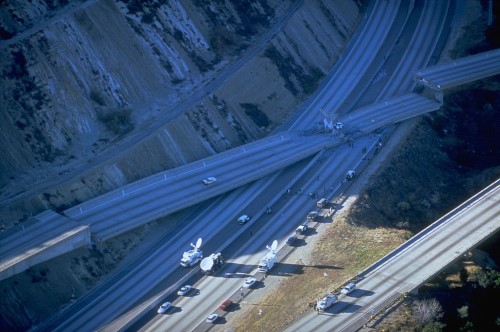
A graduate certificate in sustainable tourism
The School of Community Resources and Development offers a Graduate Certificate in Sustainable Tourism online. This program focuses on sustainable management and practices in the tourism sector. This certificate program targets professionals in tourism who are looking to advance their careers or make a change. The program teaches students how to build sustainable destinations and the business and environmental aspects that sustain sustainable tourism.
This certificate program is focused on managing food and environment resources, while also enhancing skills in preservation of ecosystems. Students will be able to create and implement sustainable initiatives, while taking into account the perspectives and needs of all stakeholders. Students will also be able to use their practical skills in communication and collaboration for their future jobs.
Executive master in sustainability leadership
Arizona State University's Executive Masters of Sustainability Leadership degree offers a degree in sustainability leadership. The program integrates research and theory with practical application. Leaders from academia and industry designed the course. It is focused on acquiring the skills and knowledge required to address current issues and find innovative solutions.
The ASU School of Sustainability has a wide range of executive and academic programs that focus on sustainability. This program offers both graduate and undergraduate degrees as well as professional certificates and tailored training for businesses. There are electives in the program that can be used to improve leadership skills for business professionals. The program prepares graduates to lead companies that adopt sustainable practices, large and small.
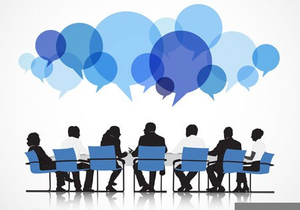
There are two core courses and four themes. Students have the opportunity to live in major US cities for a week and interact with other students. Students will also be planning their capstone project in sustainability during this time. Students also have the option of six credit hours in 500-level electives.
FAQ
What is a basic management tool that can be used for decision-making?
A decision matrix can be a simple, but effective tool to assist managers in making decisions. It allows them to think through all possible options.
A decision matrix is a way to organize alternatives into rows and columns. It is easy to see how each option affects the other options.
The boxes on the left hand side of this matrix represent four possible choices. Each box represents an alternative. The top row displays the current situation, and the bottom row shows what might happen if nothing is done.
The effect of Option 1 can be seen in the middle column. It would translate into an increase in sales from $2million to $3million.
The following columns illustrate the impact of Options 2 and 3. These positive changes result in increased sales of $1 million and $500,000. But, they also have some negative consequences. For instance, Option 2 increases cost by $100 thousand while Option 3 reduces profits by $200 thousand.
The final column shows results of choosing Option 4. This would result in a reduction of sales of $1 million.
The best part about using a decision matrix to guide you is that you don’t need to keep track of which numbers go where. Simply look at the cells to instantly determine if one choice is better than the other.
The matrix already does all the work. It is as simple a matter of comparing all the numbers in each cell.
Here's an example of how you might use a decision matrix in your business.
Decide whether you want to invest more in advertising. You'll be able increase your monthly revenue by $5000 if you do. You'll also have additional expenses up to $10,000.
Look at the cell immediately below the one that states "Advertising" to calculate the net investment in advertising. It's $15,000. Therefore, you should choose to invest in advertising since it is worth more than the cost involved.
What is the difference of a program and project?
A program is permanent while a project can be temporary.
A project usually has a specific goal and deadline.
It is often carried out by a team of people who report back to someone else.
A program is usually defined by a set or goals.
It is often implemented by one person.
What is Six Sigma?
Six Sigma employs statistical analysis to identify problems, measure them and analyze root causes. Six Sigma also uses experience to correct problems.
The first step in solving a problem is to identify it.
Next, data are collected and analyzed in order to identify patterns and trends.
The problem can then be fixed by taking corrective measures.
Final analysis of data is done to determine if the problem has been solved.
This cycle will continue until the problem is solved.
Statistics
- Hire the top business lawyers and save up to 60% on legal fees (upcounsel.com)
- 100% of the courses are offered online, and no campus visits are required — a big time-saver for you. (online.uc.edu)
- This field is expected to grow about 7% by 2028, a bit faster than the national average for job growth. (wgu.edu)
- The average salary for financial advisors in 2021 is around $60,000 per year, with the top 10% of the profession making more than $111,000 per year. (wgu.edu)
- The BLS says that financial services jobs like banking are expected to grow 4% by 2030, about as fast as the national average. (wgu.edu)
External Links
How To
How can Lean Manufacturing be done?
Lean Manufacturing processes are used to reduce waste and improve efficiency through structured methods. They were created by Toyota Motor Corporation in Japan in the 1980s. The aim was to produce better quality products at lower costs. Lean manufacturing focuses on eliminating unnecessary steps and activities from the production process. It consists of five basic elements: pull systems, continuous improvement, just-in-time, kaizen (continuous change), and 5S. Pull systems involve producing only what the customer wants without any extra work. Continuous improvement is constantly improving upon existing processes. Just-in time refers to components and materials being delivered right at the place they are needed. Kaizen means continuous improvement, which is achieved by implementing small changes continuously. Finally, 5S stands for sort, set in order, shine, standardize, and sustain. These five elements can be combined to achieve the best possible results.
Lean Production System
Six key concepts are the basis of lean production:
-
Flow - focus on moving material and information as close to customers as possible;
-
Value stream mapping is the ability to divide a process into smaller tasks, and then create a flowchart that shows the entire process.
-
Five S's: Sort, Shine Standardize, Sustain, Set In Order, Shine and Shine
-
Kanban - visual cues such as stickers or colored tape can be used to track inventory.
-
Theory of constraints - identify bottlenecks during the process and eliminate them with lean tools like Kanban boards.
-
Just-intime - Order components and materials at your location right on the spot.
-
Continuous improvement - make incremental improvements to the process rather than overhauling it all at once.