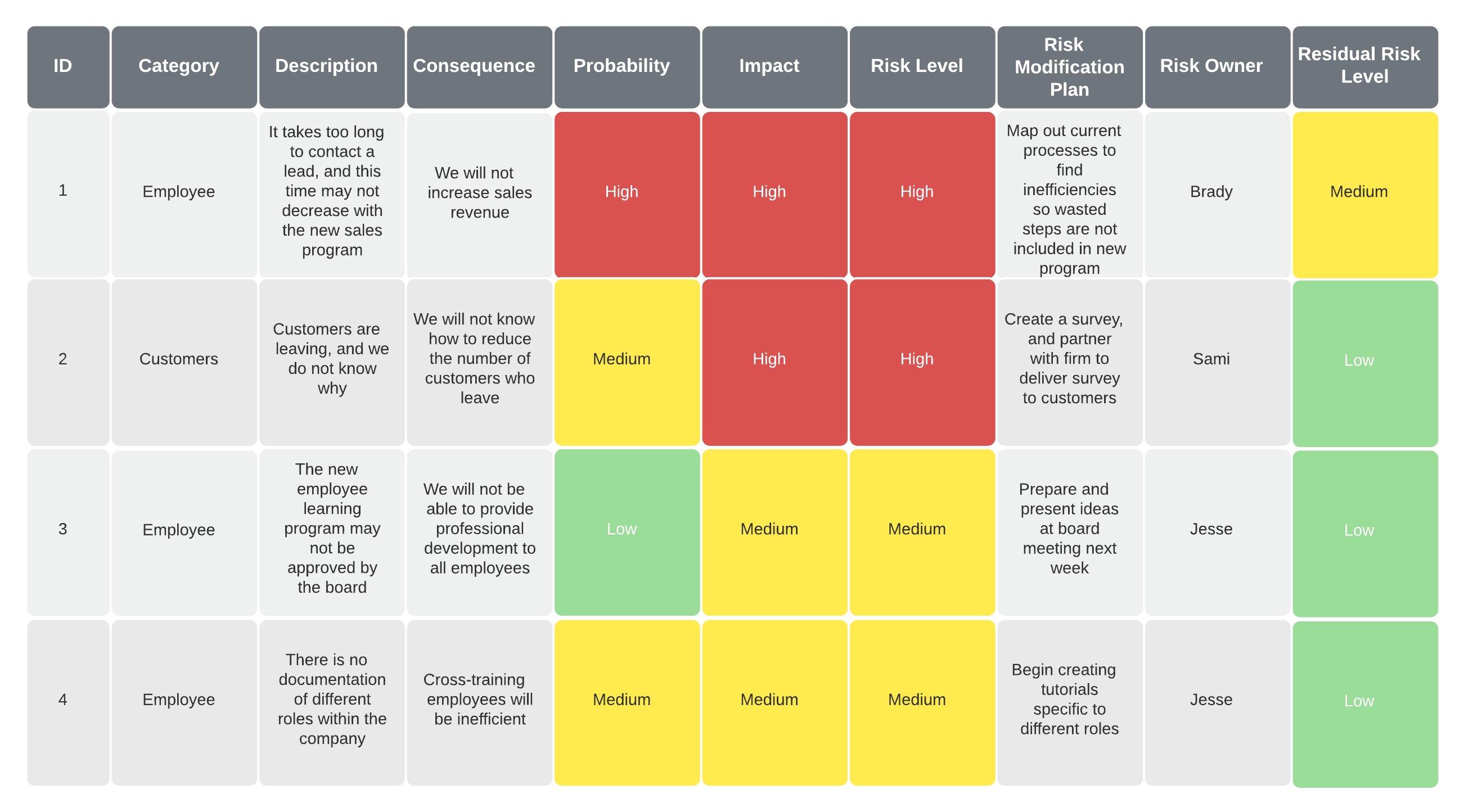
This book provides a practical and effective guide to managing global supply channels. The book is both a practical, thorough and easily understood resource that will benefit researchers and practitioners alike. This book is highly recommended. This book explains key concepts and the processes involved in strategic supply chain management. They have given a step-by–step guideline for reaching strategic supply chain goals. Both practitioners and researchers will find the book highly useful.
Demand-driven supply chains
A demand-driven supply chain is a strategic supply chain in which the entire chain responds to changes in demand. Companies can anticipate customer needs and respond to them in real-time. This is different from the traditional model where the supplier announces availability and the retailer takes delivery. This model allows companies to improve efficiency and control their inventories. In this way, demand-driven supply chains enable companies to meet customer demands faster and more efficiently.
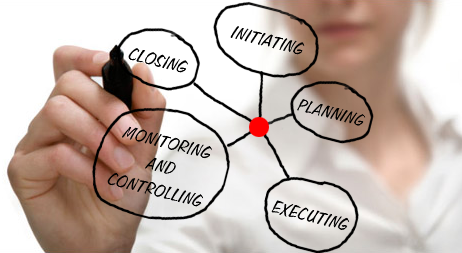
Planning
To optimize and plan the supply chain, tools that are organization-based are used. Each planning approach supports different types of decision-making. A company that is successful should have an annual strategic business plan and identify growth opportunities. Many organizations use supply chain management software to optimize and plan their supply chains. We will discuss the various planning approaches in detail below. You can pick the one you like based upon your preferred method of planning.
Execution
Strategic supply chain management is the formal approach to managing the supply chain network of an organization. The strategy is developed by the supply chain manager to maximize value, efficiency, reliability. It should be aligned with the company's overall business strategy. Effective supply chain management requires meticulous planning and execution. It is important to fully understand the role of your supply chain in your business strategy. Here are some suggestions for supply chain management success. First, establish a strategic vision for your supply chain.
Monitoring
Effective management depends on information. Ineffective management is possible when managers lack the data and tools needed to make informed decisions. As supply chains continue to grow in complexity, managers that are not diligent about monitoring the process are unprepared to handle disruptions and potential hazards. Supply chain monitoring has become a must. Monitoring your supply chain can have many benefits. Here are just few. Read on to find out how to get started.
Sustainability
It's difficult to ensure true sustainability in a supply chain. It is more challenging to achieve true sustainability in a strategic supply chain that is more complicated. The procurement team should designate an individual to be the sustainability point person and monitor the progress of suppliers. The procurement team should also create sustainability goals for suppliers and force them to achieve these goals. Transparency will be a key part of the entire process. One way to measure supplier performance effectively is to measure the number or services that contribute to the company’s sustainability goals.
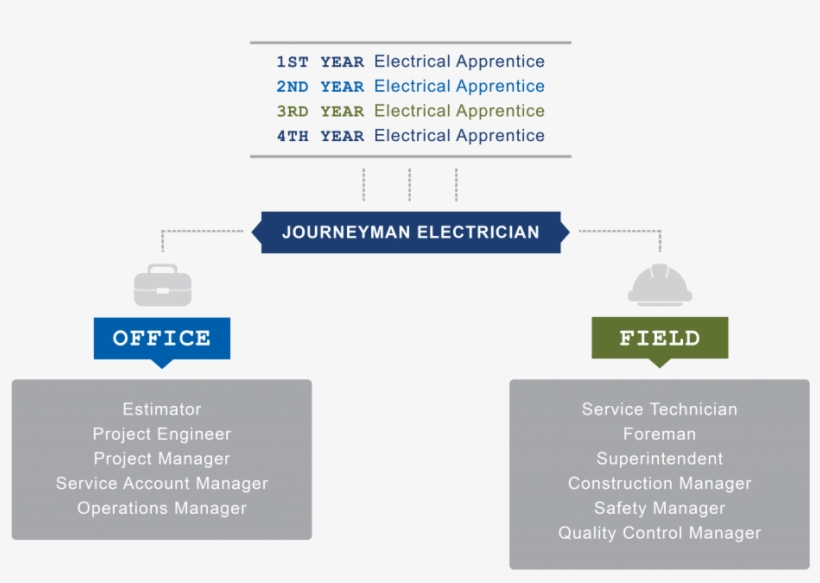
Variations based on product type
Companies must offer many products to customers to ensure optimal performance. However, they often launch product variations without knowing whether they will add complexity to their supply chains. In fact, consumer-goods companies have increased their number of products each year by 60% between 2002 and 2011. While this influx increased demand, it also raised costs throughout their supply chains. For example, in the same period, U.S. consumer-goods companies increased the number of new products they introduced annually by 60 percent. This inevitably pushed up costs in many areas of the company's supply chain, but at a steady rate of only 2.8 percent per year.
FAQ
What do we mean when we say "project management"?
This refers to managing all activities that are involved in a project's execution.
These include planning the scope and identifying the needs, creating the budget, organizing the team, scheduling the work and monitoring progress. Finally, we close down the project.
Why is it so hard to make smart business decisions?
Businesses are complex systems, and they have many moving parts. People who manage them have to balance multiple priorities while dealing with complexity and uncertainty.
Understanding how these factors impact the whole system is key to making informed decisions.
You need to be clear about the roles and responsibilities of each system. Next, consider how each piece interacts with the others.
Also, you should ask yourself if there have been any assumptions in your past behavior. If not, you might want to revisit them.
Asking for assistance from someone else is a good idea if you are still having trouble. You might find their perspective is different from yours and they may have insight that can help you find the solution.
What are management principles?
Management Concepts are the management principles and practices that managers use in managing people and resources. These topics include job descriptions, performance evaluations and training programs. They also cover human resource policies, job description, job descriptions, job descriptions, employee motivation, compensation systems, organizational structures, and many other topics.
What are the main styles of management?
There are three main management styles: participative, laissez-faire and authoritarian. Each style is unique and has its strengths as well as weaknesses. Which style do your prefer? Why?
Autoritarian – The leader sets the direction for everyone and expects them to follow. This style is most effective when an organization is large, stable, and well-run.
Laissez faire - Each individual can decide for himself/herself. This style works best when an organization is small and dynamic.
Participative - Leaders listen to all ideas and suggestions. This style is best for small organizations where everyone feels valued.
Statistics
- The average salary for financial advisors in 2021 is around $60,000 per year, with the top 10% of the profession making more than $111,000 per year. (wgu.edu)
- 100% of the courses are offered online, and no campus visits are required — a big time-saver for you. (online.uc.edu)
- The BLS says that financial services jobs like banking are expected to grow 4% by 2030, about as fast as the national average. (wgu.edu)
- UpCounsel accepts only the top 5 percent of lawyers on its site. (upcounsel.com)
- This field is expected to grow about 7% by 2028, a bit faster than the national average for job growth. (wgu.edu)
External Links
How To
How can you use the Kaizen method?
Kaizen means continuous improvement. This Japanese term refers to the Japanese philosophy of continuous improvement that emphasizes incremental improvements and constant improvement. This is a collaborative process in which people work together to improve their processes continually.
Kaizen is one the most important methods of Lean Manufacturing. Kaizen is a concept where employees in charge of the production line are required to spot problems during the manufacturing process before they become major issues. This will increase the quality and decrease the cost of the products.
Kaizen is about making everyone aware of the world around them. It is important to correct any problems immediately if they are discovered. If someone spots a problem while at work, they should immediately report it to their manager.
Kaizen has a set of basic principles that we all follow. Always start with the end product in mind and work our way back to the beginning. In order to improve our factory's production, we must first fix the machines producing the final product. Next, we fix the machines which produce components. And finally, we fix the workers who work directly with those machines.
This method is known as kaizen because it focuses upon improving every aspect of the process step by step. We finish fixing the factory and then go back to the beginning. This continues until we achieve perfection.
Before you can implement kaizen into your business, it is necessary to learn how to measure its effectiveness. There are many methods to assess if kaizen works well. One of these ways is to check the number of defects found on the finished products. Another way is to check how much productivity has grown since kaizen was implemented.
A good way to determine whether kaizen has been implemented is to ask why. Was it just because it was the law or because you wanted to save money? You really believed it would make you successful?
Congratulations! You're now ready to get started with kaizen.