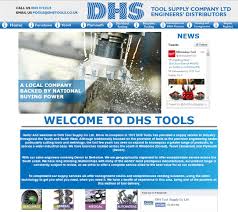
Planning and coordination are key to changing strategies. The process of creating a change plan is time-consuming and requires many people. It is important for the change agent to be able to comprehend different people's needs, and ensure that group pressures don't hinder change. He or she should also be able to understand the opinions, expectations, feelings, and motivations of everyone so that they can create an approach that addresses these needs.
Strategie of shared power
The shared power strategy is a way to change strategies and practices by engaging people at all levels in the process. By involving all levels and employee groups, the goal is to increase support for changes. It's a slow process, but the benefits outweigh the drawbacks. It is crucial to choose the right strategy for your situation and context.
This strategy requires more involvement from everyone involved in the change. It is therefore more time-consuming than others. Change agents must understand that people have differing needs and opinions and that they need to work with others to avoid group pressures. Before implementing the strategy, it is important to get to know everyone's expectations, needs, and opinions.
Target markets' cultural and social profiles
Marketing success requires that you consider the cultural and social characteristics of your target market. It is possible to have different products and services for men and women depending on their gender. Gender and roles within the family play an important role in consumer preferences. Target markets can also be understood through geography.
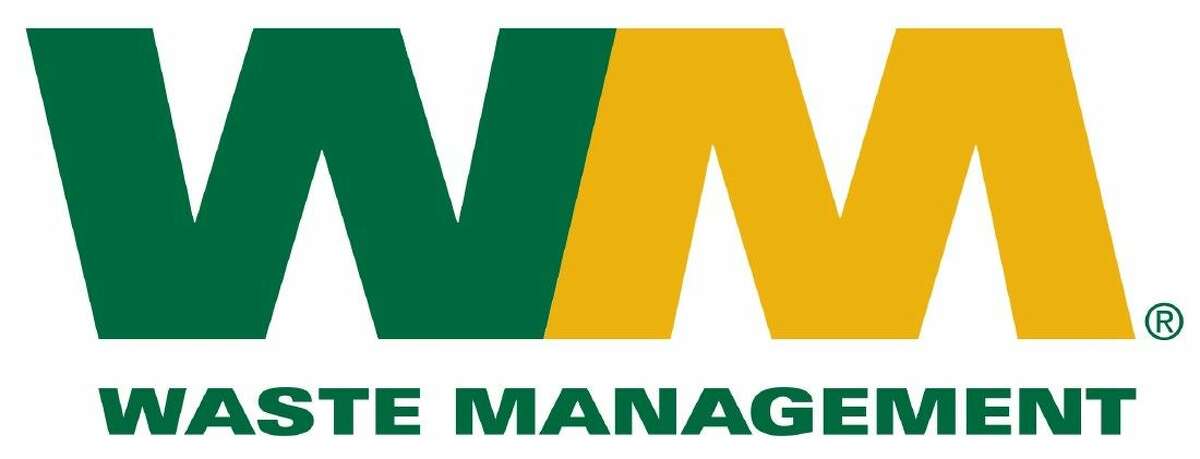
Demographics are crucial because they help you understand your customers' needs. Demographics can be defined as age, gender, occupation, income, and income. Globalization is making geographic segmentation more important. Psychographic segments, on the other hand, go beyond basic demographics to identify values, attitudes, and lifestyle.
Cost-benefit analysis
When changing strategies, a cost benefit analysis can be an invaluable tool to identify cost reductions. This analysis can also be used to help you decide which options are most effective in reaching your goals. While this process can have many advantages, there are also some limitations. Here are some things to consider when performing a cost-benefit analysis.
As the first step, you need to calculate the cost of this project. These include direct labor costs as well as indirect costs such inventory and raw materials. Overhead management costs such rent and utilities are also included. Beyond these direct costs, there are intangible and indirect costs, like the impact on employees and customers as well as delivery times. You may also need to account for opportunity costs, such as buying a plant or alternative investments. Consider regulatory risks that could impact your project.
SWOT analysis
SWOT analysis is a great tool to assess your organization's activities and plan for the future. But you must be aware of the practical implications for your proposed changes. You should also consider the long-term impact of any new market entry, such as if you are planning to enter it. Trade negotiations can take up to years to reach a definitive conclusion.
A SWOT analysis begins with identifying your strengths and weaknesses. You must also identify potential threats that could affect your operations. If your profit margin is 17% it is high compared to the 20 percent profit margins of competitors. Lack of diversification could limit your company’s potential for growth.
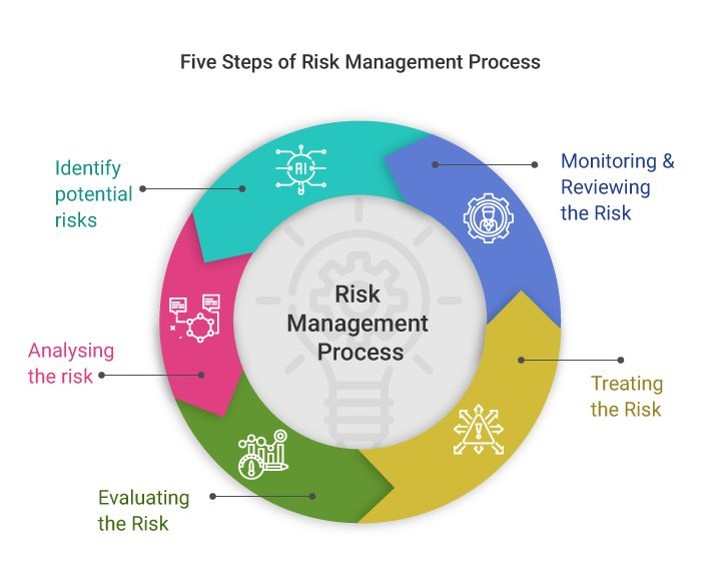
Contingency planning
Planning for the unexpected is an important step to prepare for a new strategy. The plan should be regularly reviewed to ensure the company is ready for unexpected events. Changes in management or executive leadership can make it necessary to revise the plan and consider additional changes.
When creating a contingency plan, it is important to include roles for all those involved in the process. Assign specific people to specific tasks and make sure everyone knows their role. Use a RACI-matrix to delegate different tasks to team members.
FAQ
What is TQM?
The industrial revolution was when companies realized that they couldn't compete on price alone. This is what sparked the quality movement. They had to improve efficiency and quality if they were to remain competitive.
In response to this need for improvement, management developed Total Quality Management (TQM), which focused on improving all aspects of an organization's performance. It included continual improvement processes, employee involvement, customer satisfaction, and customer satisfaction.
Why is it so hard to make smart business decisions?
Complex business systems have many moving parts. Their leaders must manage multiple priorities, as well as dealing with uncertainty.
It is important to understand the effects of these factors on the system in order to make informed decisions.
You must first consider what each piece of the system does and why. It is important to then consider how the individual pieces relate to each other.
You need to ask yourself if your previous actions have led you to make unfounded assumptions. If they don't, you may want to reconsider them.
Try asking for help from another person if you're still stuck. You may be able to see things from a different perspective than you are and gain insight that can help you find a solution.
What are the 5 management processes?
The five stages of any business are planning, execution, monitoring, review, and evaluation.
Planning means setting goals for the long-term. This includes setting goals for the future and defining what you want.
Execution is the actual execution of the plans. They must be followed by all parties.
Monitoring is a way to track progress towards your objectives. This should involve regular reviews of performance against targets and budgets.
Review events take place at each year's end. They allow for an assessment of whether all went well throughout the year. If not, changes may be made to improve the performance next time around.
After each year's review, evaluation occurs. It helps to determine what worked and what didn’t. It also provides feedback regarding how people performed.
How can we create a culture of success in our company?
A successful company culture is one that makes people feel valued and respected.
It is founded on three basic principles:
-
Everybody has something of value to share
-
People are treated with respect
-
It is possible to have mutual respect between groups and individuals
These values reflect in how people behave. They will treat others with kindness and consideration.
They will respect the opinions of others.
They can also be a source of inspiration for others.
A company culture encourages collaboration and communication.
People feel safe to voice their opinions without fear of reprisal.
They know that they will not be judged if they make mistakes, as long as the matter is dealt with honestly.
The company culture promotes honesty, integrity, and fairness.
Everyone knows that they must always tell the truth.
Everyone knows that there are rules and regulations that apply to them.
Nobody expects to be treated differently or given favors.
What are the three basic management styles?
The three major management styles are authoritarian (left-faire), participative and laissez -faire. Each style has strengths and flaws. Which style do YOU prefer? Why?
Authoritarian – The leader sets a direction and expects everyone follows it. This style is best when the organization has a large and stable workforce.
Laissez-faire: The leader lets each person decide for themselves. This style is best when the organization has a small but dynamic group.
Participative – Leaders are open to suggestions and ideas from everyone. This approach works best in small organizations where everyone feels valued.
What is the difference in Six Sigma and TQM?
The main difference between these two quality-management tools is that six-sigma concentrates on eliminating defects while total QM (TQM), focuses upon improving processes and reducing expenses.
Six Sigma stands for continuous improvement. It emphasizes the elimination or minimization of defects through statistical methods such control charts and p charts.
This method has the goal to reduce variation of product output. This is done by identifying root causes and rectifying them.
Total quality management is the measurement and monitoring of all aspects within an organization. It also involves training employees to improve performance.
It is often used to increase productivity.
What are management concepts?
Management concepts are the practices and principles managers use to manage people or resources. These include topics such as human resource policies and job descriptions, performance assessments, training programs and employee motivation.
Statistics
- Hire the top business lawyers and save up to 60% on legal fees (upcounsel.com)
- The profession is expected to grow 7% by 2028, a bit faster than the national average. (wgu.edu)
- 100% of the courses are offered online, and no campus visits are required — a big time-saver for you. (online.uc.edu)
- The BLS says that financial services jobs like banking are expected to grow 4% by 2030, about as fast as the national average. (wgu.edu)
- Your choice in Step 5 may very likely be the same or similar to the alternative you placed at the top of your list at the end of Step 4. (umassd.edu)
External Links
How To
How does Lean Manufacturing work?
Lean Manufacturing techniques are used to reduce waste while increasing efficiency by using structured methods. They were developed by Toyota Motor Corporation in Japan during the 1980s. It was designed to produce high-quality products at lower prices while maintaining their quality. Lean manufacturing focuses on eliminating unnecessary steps and activities from the production process. It is composed of five fundamental elements: continuous improvement; pull systems, continuous improvements, just-in–time, kaizen, continuous change, and 5S. Pull systems involve producing only what the customer wants without any extra work. Continuous improvement involves constantly improving upon existing processes. Just-in time refers to components and materials being delivered right at the place they are needed. Kaizen means continuous improvement, which is achieved by implementing small changes continuously. Fifth, the 5S stand for sort, set up in order to shine, standardize, maintain, and standardize. These five elements can be combined to achieve the best possible results.
The Lean Production System
The lean production system is based on six key concepts:
-
Flow - The focus is on moving information and material as close as possible to customers.
-
Value stream mapping is the ability to divide a process into smaller tasks, and then create a flowchart that shows the entire process.
-
Five S's, Sort, Set in Order, Shine. Standardize. and Sustain.
-
Kanban is a visual system that uses visual cues like stickers, colored tape or stickers to keep track and monitor inventory.
-
Theory of Constraints - Identify bottlenecks in the process, and eliminate them using lean tools such kanban boards.
-
Just-in Time - Send components and material directly to the point-of-use;
-
Continuous improvement - incremental improvements are made to the process, not a complete overhaul.