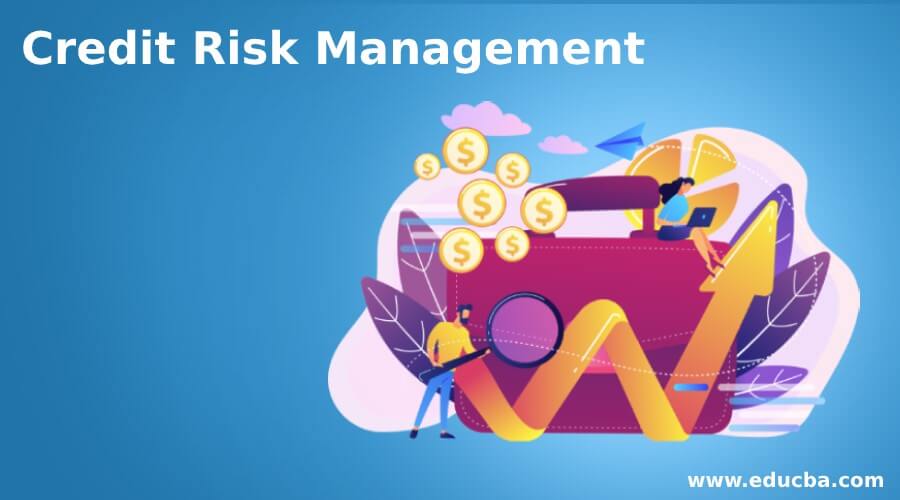
Modern HR practices are essential in today's fast-paced world. This means keeping pace with the expectations of all stakeholders and staying ahead of technologies. A variety of principles can be applied to HR departments to improve their performance. Here are just a few.
Employee orientation
Employee orientation can make it easier for new employees to feel comfortable and prepared for their new role. It can also be an effective way to reduce the turnover of new employees. The orientation process enables new employees to be familiar with the company's procedures and policies. This helps them transition smoothly into the organization. Providing clear communication of expectations is also important. Having a formal, engaging orientation helps new employees start quickly and contributes to lower turnover.
Performance management
Performance management principles can be used to create high-performing organizations. This is a continuous process that aims to align the efforts of employees with the firm's goals. To keep employees on track, it is essential to establish clear objectives and criteria. It can also help you reduce costs, increase productivity, and improve the company's overall results.
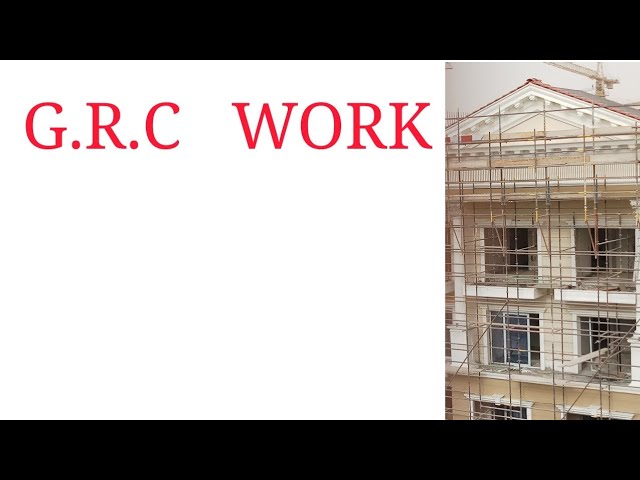
Succession planning
Succession planning can be a process that will help you to develop new leaders in your company. It starts by identifying the gaps in knowledge and skills within your team. You can then create a learning program to address these gaps. It's also important to have regular performance review meetings and communicate these areas with others.
Integration
Human resource management involves the maximization of scarce resources. This discipline seeks to optimize the organisation's use of human capital and improve its productivity. Construction has experienced a shortage of skilled labor over the past few years. This shortage is predicted to triple over the next decade, which will impact the productivity of the entire sector.
Staffing levels
A key part of human resource management is staffing levels. It's important to have the right number of employees for the right type of work. Managers should discuss their staffing requirements with other managers to determine the ideal level of staff. A company's success and growth can be impacted by the right number of employees.
Objectivity
Managers must follow the objective management principle. They should avoid bias and favoritism. This means that a manager should not prefer one employee to another. For workplace conflicts to be prevented, it is vital that employees are objective.
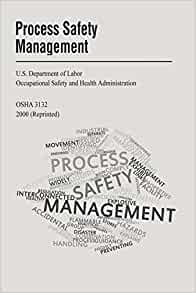
Non-monetary rewards
Employee retention and engagement strategies should include non-monetary rewards. They can have the same impact as monetary rewards but are much less costly than monetary. Non-monetary rewards promote employee interaction, encourage positive and negative feedback, provide employees with opportunities to grow in the company, and are less expensive than monetary rewards. These rewards are attractive to employees of millennials and those with gen Z backgrounds. They value these types rewards more than monetary rewards.
FAQ
Why is it important for companies to use project management techniques?
Project management techniques are used in order to ensure projects run smoothly, and that deadlines are met.
This is due to the fact that most businesses rely heavily upon project work in order to produce goods, and services.
These projects require companies to be efficient and effective managers.
Companies can lose time, money, and reputation if they don't have a good project management system.
Which kind of people use Six Sigma
Six Sigma is well-known to those who have worked in operations research and statistics. However, anyone involved in any aspect of business can benefit from using it.
It is a commitment-intensive task that requires strong leadership skills.
What is TQM?
The industrial revolution led to the birth and growth of the quality movement. Manufacturing companies realized they couldn't compete solely on price. They needed to improve the quality and efficiency of their products if they were to be competitive.
Management realized the need to improve and created Total Quality Management, which focused on improving all aspects within an organization's performance. It included continuous improvement and employee involvement as well as customer satisfaction.
What does the term "project management” mean?
We mean managing the activities involved in carrying out a project.
These include planning the scope and identifying the needs, creating the budget, organizing the team, scheduling the work and monitoring progress. Finally, we close down the project.
What is Six Sigma?
It's a strategy for quality improvement that emphasizes customer care and continuous learning. This is an approach to quality improvement that uses statistical techniques to eliminate defects.
Motorola's 1986 efforts to improve manufacturing process efficiency led to the creation of Six Sigma.
It was quickly adopted by the industry and many companies are now using six-sigma to improve product design, production, delivery, customer service, and product design.
Six Sigma is so popular.
Six Sigma is easy to implement and can produce significant results. It provides a framework that allows for improvement and helps companies concentrate on what really matters.
Statistics
- The BLS says that financial services jobs like banking are expected to grow 4% by 2030, about as fast as the national average. (wgu.edu)
- Hire the top business lawyers and save up to 60% on legal fees (upcounsel.com)
- This field is expected to grow about 7% by 2028, a bit faster than the national average for job growth. (wgu.edu)
- UpCounsel accepts only the top 5 percent of lawyers on its site. (upcounsel.com)
- Our program is 100% engineered for your success. (online.uc.edu)
External Links
How To
How can you implement the Kaizen technique?
Kaizen means continuous improvement. The term was coined in the 1950s at Toyota Motor Corporation and refers to the Japanese philosophy emphasizing constant improvement through small incremental changes. It is a process where people come together to improve their processes.
Kaizen is one the most important methods of Lean Manufacturing. The concept involves employees responsible for manufacturing identifying problems and trying to fix them before they become serious issues. This will increase the quality and decrease the cost of the products.
Kaizen is a way to raise awareness about what's happening around you. So that there is no problem, you should immediately correct it if something goes wrong. It is important that employees report any problems they see while on the job to their managers.
When doing kaizen, there are some principles we must follow. The end product is always our starting point and we work toward the beginning. We can improve the factory by first fixing the machines that make it. We then fix the machines producing components, and the machines producing raw materials. Then, we fix those who work directly with the machines.
This is known as "kaizen", because it emphasizes improving each step. After we're done with the factory, it's time to go back and fix the problem.
Before you can implement kaizen into your business, it is necessary to learn how to measure its effectiveness. There are many ways to tell if kaizen is effective. Another method is to see how many defects are found on the products. Another way is to see how much productivity has increased since implementing kaizen.
If you want to find out if your kaizen is actually working, ask yourself why. Is it because the law required it or because you want to save money. Did you really believe it would lead to success?
Let's say you answered yes or all of these questions. Congratulations! You're now ready to get started with kaizen.