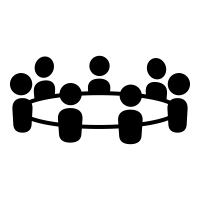
Management of supply chain risk can involve many different types of risks. These risks are related to either the demand for a particular product or the supply chain of raw materials. Demand risks happen when a business underestimates the demand for a product, while supply risks arise when raw materials do not arrive on time. Both of these risk factors can affect the flow of products. In the supply chain, there can be environmental risks due to social, political, or environmental issues.
Cybersecurity is an essential component of managing supply chain risks
Supply chain risk management is about cybersecurity measures to avoid cyber attacks on critical assets. These measures may include developing a cybersecurity policy and establishing controls for suppliers. A contract should be drawn up by companies to detail their security requirements. These contracts should detail what they will do to protect your assets. To ensure sensitive information isn't misused, a supplier should not be able to meet these requirements.
Cyber threats are becoming more complex as the supply chain grows. It is important to assess and mitigate them. Cyber threats can occur at any stage of the chain, and their impact can be devastating to a company's financial, brand, and operational health. Organizations must address cybersecurity concerns at every stage in the supply chain.
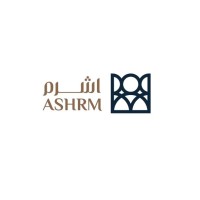
It takes a cross functional team
To manage risk in supply chains, you need a cross-functional group. This strategy should include preparations, response, as well recovery. Preparation means identifying high risk areas and creating contingency planning to address them. Prioritizing risks according severity and likelihood should be part of the plan. Visibility is another important aspect of a supply chain management strategy.
Despite the critical importance of supply-chain risk management, executives have been slow in addressing it. A survey of 639 executives from multiple industries and locations found that 71% of respondents felt their companies are more vulnerable to supply chain disruptions than they were 2 years ago. Additionally, 72 percent expect the risks to increase. Although the government has created several agencies to manage supply chain risk, the private industry is still looking for a proven way to minimize business disruption.
Supply chain boards that are effective review the major risks in the supply chain to identify mitigation steps. Each participant can take ownership of the mitigation steps during the review. One example is a procurement representative who determines the qualifications and onboarding of a new supplier.
Technology is required
As organizations try to reduce costs and build resilience, they are rethinking their approaches to supply chain risk management. They're turning to technology to improve visibility and reduce risk. Companies can build stronger supply chains and global networks with the right technology. But, in order to maximize the technology's benefits, companies must have access to accurate data. These are essential for companies to effectively manage supply chain risk.
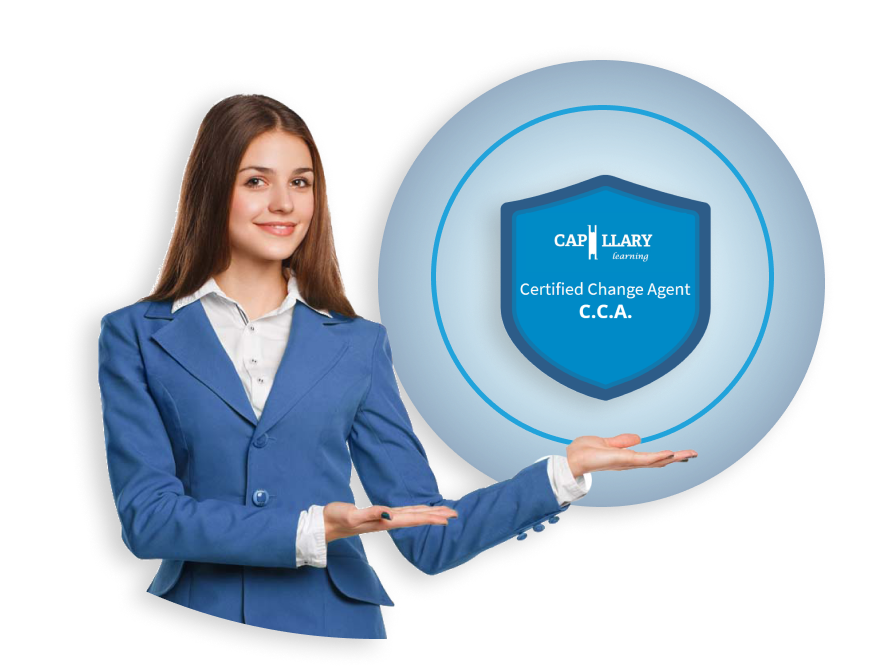
Supply chain risk management is a complex and multifaceted subject. A recent survey of 639 industry leaders found that 71% thought their supply chain was more vulnerable than it used to be and that the risk would increase. The United States government established a variety of agencies to address supply chains risk. One of these agencies is the Protecting Critical Technology Task Force, which is part of the Department of Defense. Private companies are also looking for proven methods to reduce the negative impact of supply chain risk on their businesses.
FAQ
What can a manager do to improve his/her management skillset?
Good management skills are essential for success.
Managers must monitor the performance of subordinates constantly.
If you notice your subordinate isn't performing up to par, you must take action quickly.
You should be able pinpoint what needs to improve and how to fix it.
What is TQM and how can it help you?
When manufacturing companies realized that price was not enough to compete, the industrial revolution brought about the quality movement. They needed to improve the quality and efficiency of their products if they were to be competitive.
In response to this need for improvement, management developed Total Quality Management (TQM), which focused on improving all aspects of an organization's performance. It included continuous improvement processes, employee involvement, and customer satisfaction.
What is Six Sigma?
It's an approach to quality improvement that emphasizes customer service and continuous learning. The objective is to eliminate all defects through statistical methods.
Motorola invented Six Sigma in 1986 as part its efforts to improve manufacturing.
It was quickly adopted by the industry and many companies are now using six-sigma to improve product design, production, delivery, customer service, and product design.
What are the steps involved in making a decision in management?
Managers have to make complex decisions. This involves many factors including analysis, strategy and planning, implementation, measurement and evaluation, feedback, feedback, and others.
When managing people, the most important thing to remember is that they are just human beings like you and make mistakes. You can always improve your performance, provided you are willing to make the effort.
This video shows you how management makes decisions. We will discuss the various types of decisions, and why they are so important. Every manager should be able to make them. Here are some topics you'll be learning about:
What are some of the common mistakes made by managers?
Managers can make their jobs more difficult than necessary.
They may not be able to delegate enough responsibility to staff or provide adequate support.
Managers often lack the communication skills necessary to motivate and guide their teams.
Some managers create unrealistic expectations for their teams.
Some managers may try to solve every problem themselves instead of delegating responsibility to others.
What is the difference between Six Sigma Six Sigma and TQM?
The main difference in these two quality management tools lies in the fact that six sigma is focused on eliminating defects and total quality management (TQM), emphasizes improving processes and reducing costs.
Six Sigma is a method for continuous improvement. This method emphasizes eliminating defects using statistical methods such p-charts, control charts, and Pareto analysis.
This method aims to reduce variation in product production. This is achieved by identifying and addressing the root causes of problems.
Total quality management involves measuring and monitoring all aspects of the organization. It also includes the training of employees to improve performance.
It is often used as a strategy to increase productivity.
How do you manage your employees effectively?
Effectively managing employees requires that you ensure their happiness and productivity.
This includes setting clear expectations for their behavior and tracking their performance.
Managers need clear goals to be able to accomplish this.
They must communicate clearly with their staff. And they need to ensure that they reward good performance and discipline poor performers.
They will also need to keep records about their team's activities. These include:
-
What did we accomplish?
-
How much work was put in?
-
Who did it?
-
How did it get done?
-
Why was it done?
This information can help you monitor your performance and to evaluate your results.
Statistics
- Hire the top business lawyers and save up to 60% on legal fees (upcounsel.com)
- The BLS says that financial services jobs like banking are expected to grow 4% by 2030, about as fast as the national average. (wgu.edu)
- As of 2020, personal bankers or tellers make an average of $32,620 per year, according to the BLS. (wgu.edu)
- This field is expected to grow about 7% by 2028, a bit faster than the national average for job growth. (wgu.edu)
- Your choice in Step 5 may very likely be the same or similar to the alternative you placed at the top of your list at the end of Step 4. (umassd.edu)
External Links
How To
How can I obtain my Six Sigma license
Six Sigma is a tool for quality management to improve processes and increase efficiency. It's a methodology that helps companies achieve consistent results from their operations. The name "Sigmas" comes from the Greek words "sigmas", meaning "six". Motorola developed this process in 1986. Motorola recognized the need to standardize manufacturing processes in order to produce better products at a lower cost. Because of the number of people involved in the work, they had problems maintaining consistency. They decided to use statistical tools like control charts and Pareto analysis to solve the problem. These techniques would be applied to every aspect of the operation. This would allow them to make any necessary changes. Three main steps are involved when you're trying to go through the whole process of getting your Six Sigma certification. First, you need to determine if your qualifications are valid. Before you take any exams, you'll need to take some classes. You can then start taking the tests once you have completed those classes. You will want to remember everything you learned in the class. Then, you'll be ready to take the test. If you pass, you'll get certified. Final, your certifications can be added to you resume.