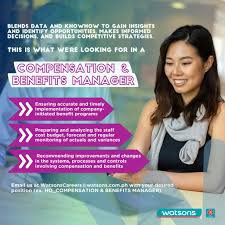
Arapahoe Community College in Littleton is a Colorado public institution. It was founded in 1965, making it one of the first community colleges in the Denver area. It offers many undergraduate programs. Learn more about the courses and requirements for an ACC Degree if you're interested in pursuing it.
Getting an ACC degree
An ACC degree is a great option to get started in your career and make a mark on the job market. The college offers a variety of academic programs that will prepare you for either immediate employment or transfer into a four-year university. There may be prerequisite courses that you need before you are allowed to enroll in a program. Admission requirements will vary depending on the program. Both returning students, as well as newcomers, are eligible to enroll.
The college offers over 100 programs in 10 subjects. Associate of Arts degrees, university transfer credits and career-technical certificates can be earned. Austin Community College offers many options for high school students. The college offers courses in a variety settings, including hands-on labs and non-traditional classroom settings. Additionally, the college offers career services as well as field trips and cultural events.
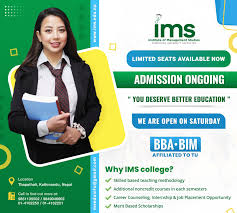
Required courses
For students to be awarded a degree from the Arapahoe Community College they must take certain courses. These courses are described in the college’s Catalog. Arapahoe may also modify these policies at any moment. For the most current information, students should visit the college's website.
The college offers many programs. If you're interested in an Associate of Science degree you have the option of choosing from Business, Art History and Psychology. An associate degree can be earned in Spanish, or in another language.
Acceptance to a 4-year university
Arapahoe Community College (located in Littleton Colorado) is a publicly funded college. It is home to 11,544 students. The academic calendar is semester-based. It offers many degree programs in 16 different areas. Many of these degrees can be transferred to 4-year universities.
ACC can help you get a career credential or to continue your education. The courses can be taken online or at the high school level. While pursuing your degree, you can also earn your workforce credential.
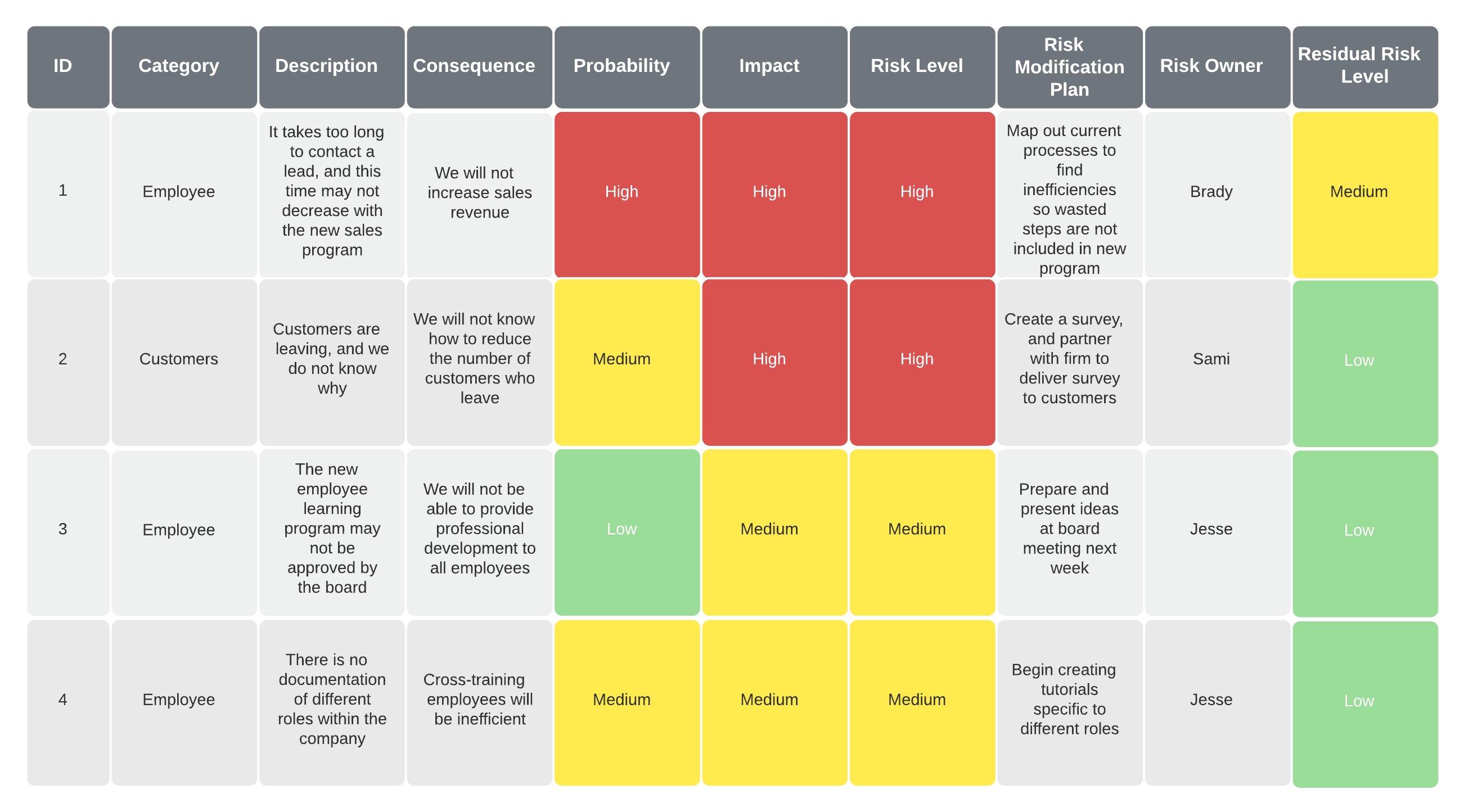
Study abroad options at ACC
The study abroad program at Arapahoe Community College offers a number of options to students seeking to gain global experience. These programs provide guided learning and cultural engagement. They are designed to develop students' personal skills and help them reach their professional and educational goals. A Study Abroad Club can also be found at the college. This club meets regularly to encourage international understanding as well as cultural diversity.
The college offers many study abroad options, ranging from programs in Western Europe to those in the far reaches Asia. It has previously offered programs in Vietnam, Beijing, Costa Rica, and Australia. Many programs are tied to particular courses and can often be completed within one week or one semester.
FAQ
Why is it so important for companies that they use project management techniques
Project management techniques can be used to ensure smooth project execution and meeting deadlines.
Because most businesses depend heavily on project work to produce goods or services,
Companies need to manage these projects efficiently and effectively.
Without effective project management, companies may lose money, time, and reputation.
What's the difference between Six Sigma and TQM?
The main difference between these two quality management tools is that six sigma focuses on eliminating defects while total quality management (TQM) focuses on improving processes and reducing costs.
Six Sigma stands for continuous improvement. This approach emphasizes eliminating defects through statistical methods like control charts, Pareto analysis, and p-charts.
This method seeks to decrease variation in product output. This is done by identifying root causes and rectifying them.
Total quality management refers to the monitoring and measurement of all aspects in an organization. It also involves training employees to improve performance.
It is often used to increase productivity.
How to effectively manage employees
The key to effective management of employees is ensuring their happiness and productivity.
This includes setting clear expectations for their behavior and tracking their performance.
Managers must set clear goals for their employees and themselves to achieve this goal.
They should communicate clearly to staff members. They also need to make sure that they discipline and reward the best performers.
They must also keep track of the activities of their team. These include:
-
What was accomplished?
-
What was the work involved?
-
Who did it?
-
Was it done?
-
Why it was done?
This information can help you monitor your performance and to evaluate your results.
What role does a manager play in a company?
The role of a manager varies from one industry to another.
Managers generally oversee the day-today operations of a business.
He/she will ensure that the company fulfills its financial obligations.
He/she is responsible for ensuring that employees comply with all regulations and follow quality standards.
He/she plans new products and services and oversees marketing campaigns.
What is a management tool to help with decision-making?
A decision matrix, a simple yet powerful tool for managers to make decisions, is the best. It helps them to think strategically about all options.
A decision matrix allows you to represent alternatives as columns and rows. This makes it easy to see how each alternative affects other choices.
This example shows four options, each represented by the boxes on either side of the matrix. Each box represents one option. The top row depicts the current status quo, while the bottom row represents what would happen if no action was taken.
The effect of Option 1 can be seen in the middle column. In this case, it would mean increasing sales from $2 million to $3 million.
The following columns illustrate the impact of Options 2 and 3. These are good changes, they increase sales by $1million or $500,000. However, these also involve negative consequences. For instance, Option 2 increases cost by $100 thousand while Option 3 reduces profits by $200 thousand.
Finally, the last column shows the results of choosing Option 4. This would result in a reduction of sales of $1 million.
The best part of using a decision-matrix is that it doesn't require you to know which numbers belong where. It's easy to see the cells and instantly know if any one of them is better than another.
The matrix already does all the work. It is as simple a matter of comparing all the numbers in each cell.
Here's an example of how you might use a decision matrix in your business.
You need to decide whether to invest in advertising. This will allow you to increase your revenue by $5000 per month. You'll also have additional expenses up to $10,000.
You can calculate the net result of investing in advertising by looking at the cell directly below the one that says "Advertising." That number is $15 thousand. Therefore, you should choose to invest in advertising since it is worth more than the cost involved.
What is Six Sigma?
It's an approach to quality improvement that emphasizes customer service and continuous learning. The objective is to eliminate all defects through statistical methods.
Six Sigma was developed at Motorola in 1986 as part of its efforts to improve manufacturing processes.
The idea spread quickly in the industry. Today many organizations use six-sigma techniques to improve product design.
How does a manager develop his/her management skills?
By practicing good management skills at all times.
Managers should monitor the performance and progress of their subordinates.
You must quickly take action if your subordinate fails to perform.
You should be able pinpoint what needs to improve and how to fix it.
Statistics
- This field is expected to grow about 7% by 2028, a bit faster than the national average for job growth. (wgu.edu)
- The BLS says that financial services jobs like banking are expected to grow 4% by 2030, about as fast as the national average. (wgu.edu)
- UpCounsel accepts only the top 5 percent of lawyers on its site. (upcounsel.com)
- Your choice in Step 5 may very likely be the same or similar to the alternative you placed at the top of your list at the end of Step 4. (umassd.edu)
- 100% of the courses are offered online, and no campus visits are required — a big time-saver for you. (online.uc.edu)
External Links
How To
What is Lean Manufacturing?
Lean Manufacturing techniques are used to reduce waste while increasing efficiency by using structured methods. These processes were created by Toyota Motor Corporation, Japan in the 1980s. The primary goal was to make products with lower costs and maintain high quality. Lean manufacturing eliminates unnecessary steps and activities from a production process. It is composed of five fundamental elements: continuous improvement; pull systems, continuous improvements, just-in–time, kaizen, continuous change, and 5S. Pull systems involve producing only what the customer wants without any extra work. Continuous improvement refers to continuously improving existing processes. Just-in-time refers to when components and materials are delivered directly to the point where they are needed. Kaizen is continuous improvement. This can be achieved by making small, incremental changes every day. Fifth, the 5S stand for sort, set up in order to shine, standardize, maintain, and standardize. These five elements are used together to ensure the best possible results.
The Lean Production System
The lean production system is based on six key concepts:
-
Flow: The goal is to move material and information as close as possible from customers.
-
Value stream mapping: This is a way to break down each stage into separate tasks and create a flowchart for the entire process.
-
Five S’s - Sorted, In Order. Shine. Standardize. And Sustain.
-
Kanban - visual cues such as stickers or colored tape can be used to track inventory.
-
Theory of constraints: identify bottlenecks in your process and eliminate them using lean tools, such as kanban board.
-
Just-in time - Get components and materials delivered right at the point of usage;
-
Continuous improvement - Make incremental improvements rather than overhauling the entire process.