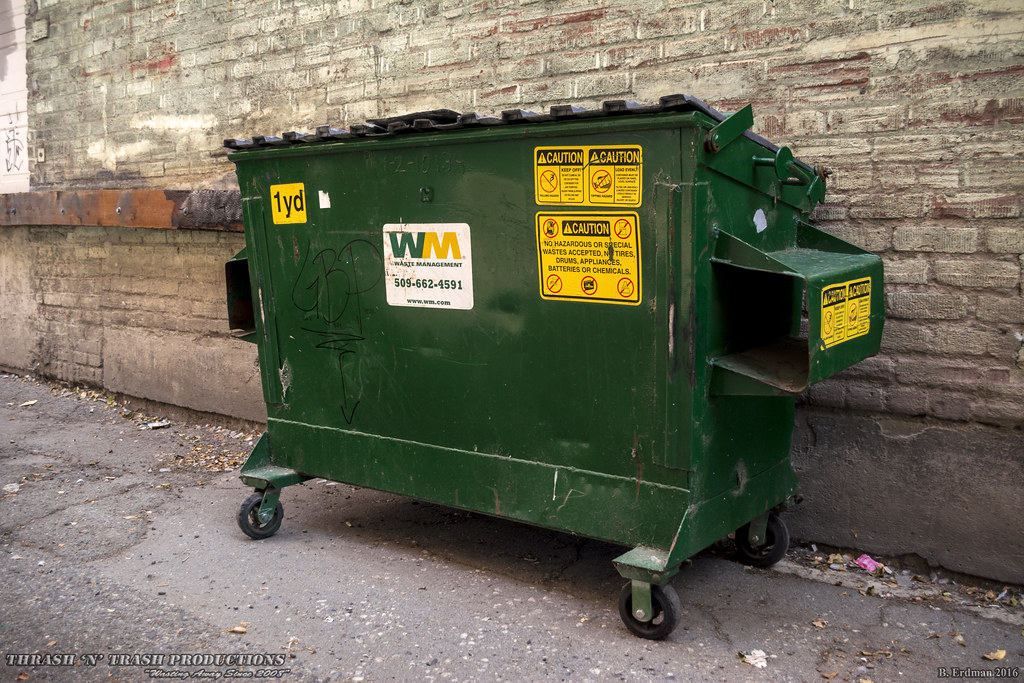
Governance, risk and compliance are three of the three legs that make up the Three-legged stool. These three legs are critical to the success of every business, no matter its industry. Here's a quick look at what GRC means and how you can apply it to your business. This isn't just paperwork.
Governance, risk and compliance
An organization's overall performance depends on its governance, risk, compliance (GRC), services. They help organizations identify and manage risks and ensure compliance with all laws and regulations. They also help companies protect their brand reputation and establish sustainable practices. HCL has a rich history in GRC. Their experienced practitioners can help you implement GRC best-practices.
GRC can take many forms, but the goal is the same: to better integrate and sync information across different disciplines in order to improve reporting, information sharing, or avoid duplicates. GRC usually includes corporate governance, corporate risk management, and corporate compliance. GRC is becoming more important as organizations grow and reach critical sizes. GRC should be effective because it integrates across disciplines. These disciplines all have the same people, processes, and technologies.
Stool with three legs
GRC encompasses the process of ensuring compliance with all industry and regulatory requirements. These requirements aren't always the same and some processes overlap. It is important to pay equal attention to each leg in order to balance the GRC process. A stool that has one leg too short or too long will not be functional and stable. Similarly, the business platform should have three equal legs to be effective.
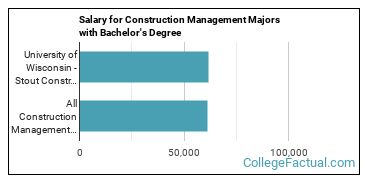
Financial planners frequently use the term "three-legged stool" to describe retirement income. This refers three different sources for retirement income, namely, employer pension, employee saving, and social security. This system was once sufficient. But it doesn't stand alone anymore. In the twenty-first century, many workers do not have the same retirement benefits as their counterparts did in the past. Because of this, the three-legged stool became obsolete. Pensions are still available for certain workers, but the burden of investing them has fallen on individuals.
Integrative approach to managing risk
Integrative risk management is a combination risk management techniques, processes and guidelines. Its key features are the identification of risks and their associated exposures. Its purpose serves to ensure effective risk management across the enterprise. It establishes roles for all stakeholders and provides guidelines. These guidelines and teams assess and monitor the risks associated a company’s product or portfolio. They then set appropriate limits for each.
Integrative risk management strategies take into account all possible outcomes to a business strategy. Traditional risk management only considers the risks involved with risks. Integrative risk management, however, also considers potential business benefits. This integrated approach to risk management improves decision making. Businesses can identify and communicate more risks to their business units and IT teams by having better risk management. An organization that has an IRM strategy is better equipped to handle any negative outcomes. This is essential for its continued success.
Benefits
GRC implementation can be as simple as setting goals. This is a critical step and can make the difference of success or failure. It will help you understand what GRC is for your company and the people involved in it's implementation. GRC can be made successful by getting the right people onboard early.
GRC can help you streamline your business. It helps reduce duplication of work and eliminates wasteful spending. It can also increase productivity and motivation for your employees. A centralized GRC approach is a great way to improve the quality of information and speed up decision making.
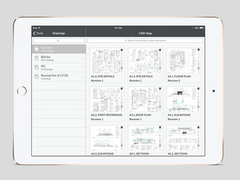
Challenges
GRC can be described as a business-wide approach in managing risk. Its pillars are people, processes and information. These elements need to be integrated to ensure compliance and effective risk management. Organizations could face new data-privacy regulations as well as internal data-protection control requirements. GRC strategies can be integrated to remove silos, foster collaboration and help organizations achieve their goals.
GRC strategies are more common because they allow for accountability, security, efficiency, visibility, and accountability. However, it is crucial to recognize the issues and find solutions.
FAQ
What are the most important management skills?
Business owners need to have management skills, no matter how small or large they may be. They are the ability to manage people and finances, space, money, and other factors.
Management Skills are also needed when you're setting goals and objectives, planning strategies, leading teams, motivating employees, resolving problems, creating policies and procedures, and managing change.
There are so many managerial tasks!
What is the difference between Six Sigma Six Sigma and TQM?
The main difference between these two quality management tools is that six sigma focuses on eliminating defects while total quality management (TQM) focuses on improving processes and reducing costs.
Six Sigma is a method for continuous improvement. It emphasizes the elimination and improvement of defects using statistical methods, such as control charts, P-charts and Pareto analysis.
This method aims to reduce variation in product production. This is accomplished through identifying and correcting root causes.
Total quality management is the measurement and monitoring of all aspects within an organization. It also involves training employees to improve performance.
It is often used to increase productivity.
Which kind of people use Six Sigma
People who have worked with statistics and operations research will usually be familiar with the concepts behind six sigma. Anybody involved in any aspect or business can benefit.
It requires high levels of commitment and leadership skills to be successful.
What is Six Sigma?
This is a method of quality improvement that emphasizes customer service, continuous learning, and customer service. The objective is to eliminate all defects through statistical methods.
Motorola developed Six Sigma in 1986 to help improve its manufacturing processes.
The idea spread quickly throughout the industry, and today, many organizations are using six sigma methods to improve product design, production, delivery, and customer service.
What role does a manager have in a company's success?
Different industries have different roles for managers.
In general, a manager controls the day-to-day operations of a company.
He/she is responsible for ensuring that the company meets all its financial obligations and produces the goods or services customers want.
He/she will ensure that employees follow all rules and regulations, and adhere to quality standards.
He/she plans new products and services and oversees marketing campaigns.
What is the difference in a project and program?
A project is temporary; a program is permanent.
A project has usually a specified goal and a time limit.
It is usually done by a group that reports back to another person.
A program is usually defined by a set or goals.
It is usually done by one person.
What are the four major functions of Management?
Management is responsible in planning, organizing and directing people and resources. It includes the development of policies and procedures as well as setting goals.
Organizations can achieve their goals through management. This includes leadership, coordination, control and motivation.
The following are the four core functions of management
Planning - Planning involves determining what needs to be done.
Organizing: Organizing refers to deciding how things should work.
Directing - Directing means getting people to follow instructions.
Controlling – Controlling is the process of ensuring that tasks are completed according to plan.
Statistics
- 100% of the courses are offered online, and no campus visits are required — a big time-saver for you. (online.uc.edu)
- Our program is 100% engineered for your success. (online.uc.edu)
- UpCounsel accepts only the top 5 percent of lawyers on its site. (upcounsel.com)
- The profession is expected to grow 7% by 2028, a bit faster than the national average. (wgu.edu)
- Hire the top business lawyers and save up to 60% on legal fees (upcounsel.com)
External Links
How To
How do I do the Kaizen Method?
Kaizen means continuous improvement. This Japanese term refers to the Japanese philosophy of continuous improvement that emphasizes incremental improvements and constant improvement. It's a process where people work together to improve their processes continuously.
Kaizen is one of Lean Manufacturing's most efficient methods. In this concept, employees who are responsible for the production line must identify problems that exist during the manufacturing process and try to solve them before they become big issues. This increases the quality of products and reduces the cost.
Kaizen is about making everyone aware of the world around them. So that there is no problem, you should immediately correct it if something goes wrong. If someone spots a problem while at work, they should immediately report it to their manager.
There are some basic principles that we follow when doing kaizen. Always start with the end product in mind and work our way back to the beginning. If we want to improve our factory for example, we start by fixing the machines that make the final product. Next, we fix the machines which produce components. And finally, we fix the workers who work directly with those machines.
This approach is called 'kaizen' because it focuses on improving everything steps by step. Once the factory is fixed, we return to the original site and work our way back until we get there.
You need to know how to measure the effectiveness of kaizen within your business. There are several ways that you can tell if your kaizen system is working. One way is to examine the amount of defects on the final products. Another method is to determine how much productivity has improved since the implementation of kaizen.
You can also find out if kaizen works by asking yourself why you decided to implement it. Was it just because it was the law or because you wanted to save money? You really believed it would make you successful?
Suppose you answered yes to any of these questions, congratulations! You are ready to start kaizen.