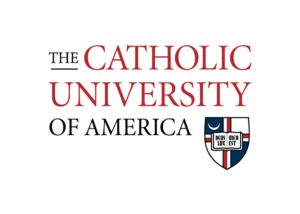
Labor relations specialists are a great career choice if you're interested in a career in the field of labor relations. A Bachelor's degree is required for this job, but you can also get a Master’s degree. In the job description of a labor relations specialist, it should specify required and preferred qualifications. A labor relations specialist's education and certification should also be spelled out in the job description.
Common duties of a labor-relations specialist
Labor relations specialists should not only have knowledge in human resources but also be skilled at problem-solving and interpersonal skills. He or she should also be adept at spreadsheets and technology. A labor relations specialist's resume can be made in just minutes. When creating your own resume, you can refer to our examples of labor relations specialist resumes.
A bachelor's is typically required for labor relations specialists. However, education requirements can vary from a high school diploma to a master's degree. Labor relations specialists work to bridge the gap between workers' and managerial expectations.
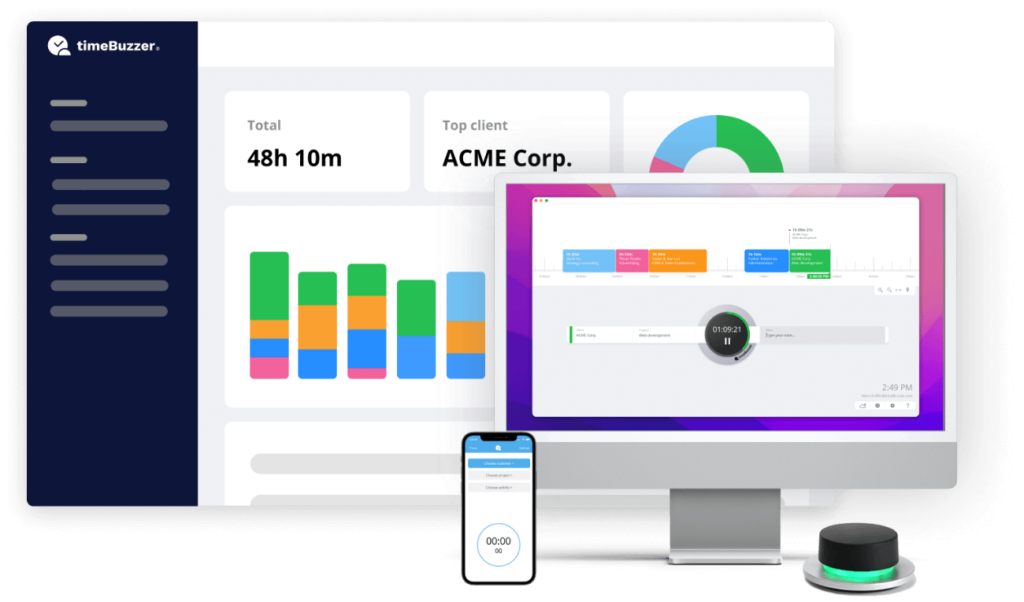
Education required
Before pursuing this career path, it is important to understand the employment laws. These laws include The Fair Labor Standards Act and National Labor Relations Act. A solid knowledge of these laws is necessary to become a labor relation specialist. For this purpose, you can take undergraduate and graduate courses in labor law. This field also offers certifications. These are optional, but will allow you to better understand the labor laws and enable you to focus your efforts on specific areas.
No matter your educational level, a labor-relations specialist must possess exceptional communication skills. They must be able communicate effectively with employees and managers. They should also be able to resolve conflicts. It is important that you review the job description for labor relations specialist in order to understand what skills and education are needed.
Earning potential
There is an increasing demand for labor relations specialists as the 21st century progresses. While the number of people leaving the profession is decreasing, there are many new jobs opening up each year. There will be 70,000 jobs available between now and 2029. It's a good place to start if you're interested. Many people who have careers in other fields can gain experience in the field and then earn a degree while working. They will be more successful if they can communicate with clients and manage negotiation.
Earning potential for labor relations specialists ranges from $64,800 to $128,600. Salaries vary based on experience and region. On average, labor relations specialists earn $74,877 per annum. New Jersey and the Utilities sector are the highest-paying areas for labor relations specialists.
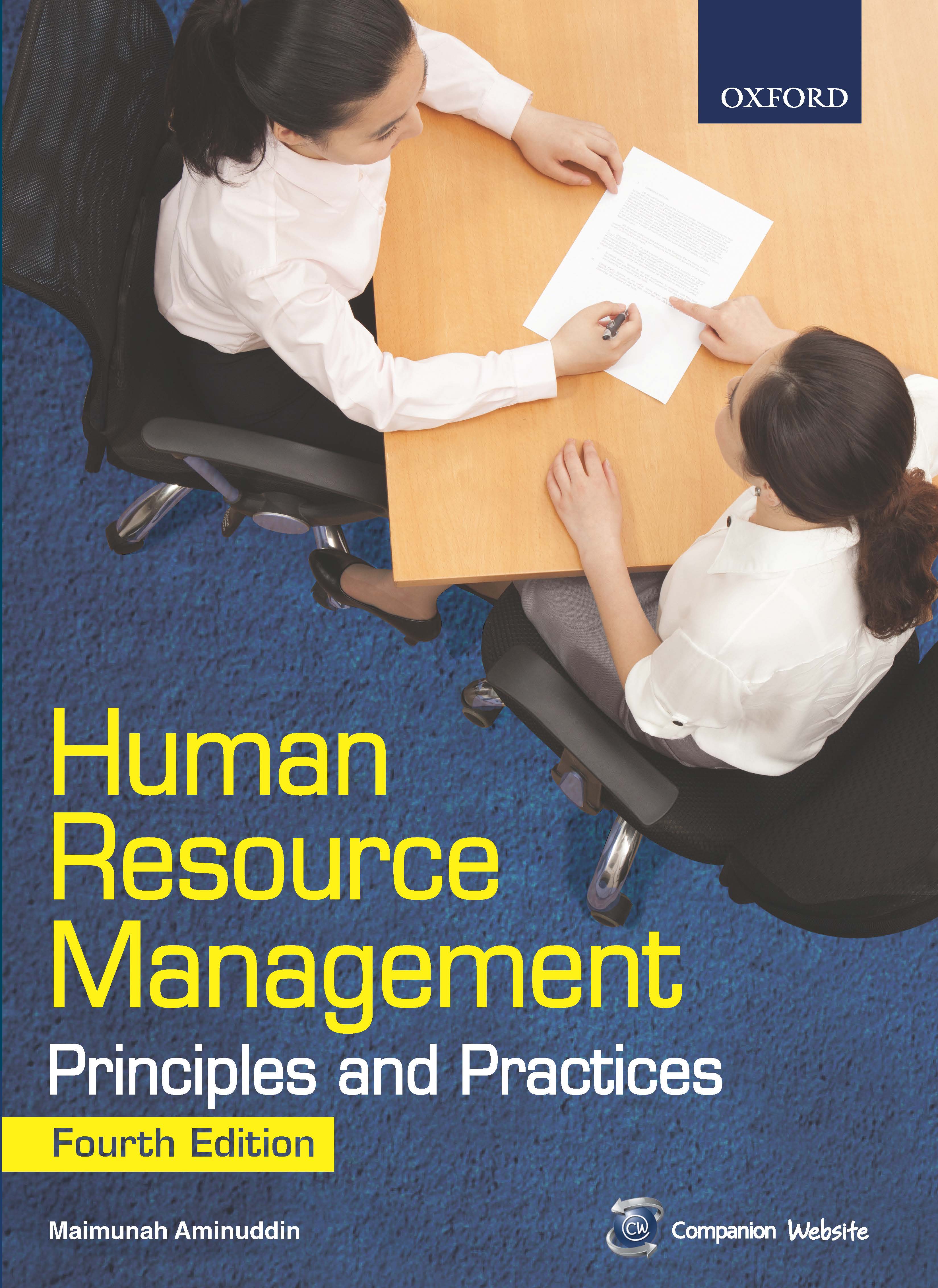
Perspectives on the job
According to U.S. Bureau of Labor Statistics. the job outlook is generally negative for labor relations experts. This is due to the decline in union membership which is expected decreases employment opportunities. Candidates with higher education or specialized certification will still have the best job prospects.
An undergraduate degree with a focus on human resources will allow you to pursue a career working in labor relations. This degree focuses both on leadership in business and the effective management employees. It covers current trends in human resources and labor relations.
FAQ
What are your main management skills
Managerial skills are crucial for every business owner, regardless of whether they run a small store in their locality or a large corporation. These skills include the ability of managing people, finances, time, space, and other factors.
Management Skills are also needed when you're setting goals and objectives, planning strategies, leading teams, motivating employees, resolving problems, creating policies and procedures, and managing change.
As you can see, there are many managerial responsibilities!
Why is it important that companies use project management methods?
Project management techniques ensure that projects run smoothly while meeting deadlines.
This is because most businesses rely heavily on project work to produce goods and services.
These projects are essential for companies.
Companies could lose their time, reputation, and money without effective project management.
How can we create a successful company culture?
A positive company culture creates a sense of belonging and respect in its people.
It's founded on three principal principles:
-
Everybody has something to offer.
-
People are treated fairly
-
It is possible to have mutual respect between groups and individuals
These values are reflected by the way people behave. They will show consideration and courtesy to others.
They will listen respectfully to the opinions of others.
And they will encourage others to share ideas and feelings.
The company culture promotes collaboration and open communication.
People feel free to express their views openly without fear of reprisal.
They are aware that mistakes can be accepted if they are treated honestly.
The company culture promotes honesty, integrity, and fairness.
Everybody knows they have to tell the truth.
Everyone recognizes that rules and regulations are important to follow.
Everyone does not expect to receive special treatment.
What is the difference in leadership and management?
Leadership is all about influencing others. Management is all about controlling others.
Leaders inspire followers, while managers direct workers.
Leaders motivate people to succeed; managers keep workers on track.
A leader develops people; a manager manages people.
What's the difference between a program and a project?
A program is permanent while a project can be temporary.
A project is usually defined by a clear goal and a set deadline.
It is often performed by a team of people, who report back on someone else.
A program will usually have a set number of goals and objectives.
It is usually done by one person.
How does a manager develop his/her management skills?
It is important to have good management skills.
Managers must continuously monitor the performance levels of their subordinates.
You must quickly take action if your subordinate fails to perform.
It is essential to know what areas need to be improved and how to do it.
Statistics
- 100% of the courses are offered online, and no campus visits are required — a big time-saver for you. (online.uc.edu)
- UpCounsel accepts only the top 5 percent of lawyers on its site. (upcounsel.com)
- The profession is expected to grow 7% by 2028, a bit faster than the national average. (wgu.edu)
- Our program is 100% engineered for your success. (online.uc.edu)
- This field is expected to grow about 7% by 2028, a bit faster than the national average for job growth. (wgu.edu)
External Links
How To
How can you implement the Kaizen technique?
Kaizen means continuous improvement. This Japanese term refers to the Japanese philosophy of continuous improvement that emphasizes incremental improvements and constant improvement. It is a process where people come together to improve their processes.
Kaizen is one the most important methods of Lean Manufacturing. In this concept, employees who are responsible for the production line must identify problems that exist during the manufacturing process and try to solve them before they become big issues. This improves the quality of products, while reducing the cost.
Kaizen is about making everyone aware of the world around them. To prevent problems from happening, any problem should be addressed immediately. Report any problem you see at work to your manager.
When doing kaizen, there are some principles we must follow. The end product is always our starting point and we work toward the beginning. We can improve the factory by first fixing the machines that make it. Next, we repair the machines that make components. Then, the machines that make raw materials. Then we fix the workers, who directly work with these machines.
This is why it's called "kaizen" because it works step-by-step to improve everything. We finish fixing the factory and then go back to the beginning. This continues until we achieve perfection.
It is important to understand how to measure the effectiveness and implementation of kaizen in your company. There are many ways to tell if kaizen is effective. One way is to examine the amount of defects on the final products. Another way is determining how much productivity increased after implementing kaizen.
Another way to know whether kaizen is working is to ask yourself why did you decide to implement kaizen. You were trying to save money or obey the law? Did you really think that it would help you achieve success?
Suppose you answered yes to any of these questions, congratulations! You're ready to start kaizen.