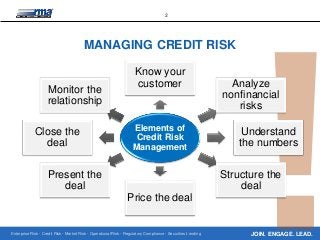
There are many journals which provide information about the latest developments in supply-chain management. The Journal of Supply Chain Management and Journal of Managing Value and Supply Chains are two examples of such publications. Some journals focus on a particular industry or sector. These journals can help you gain a better understanding of your industry and how it operates.
Journal of Supply Chain Management
The Journal of Supply Chain Management (peer-reviewed academic journal) focuses on supply chains management. It is published quarterly and covers topics in operations, marketing, and strategic management. Wiley-Blackwell is the publisher of this journal. It was first published in 1965. The Journal of Supply Chain Management covers supply chain management. It also covers organizational behavior and social network analysis.
Its goal is to bring readers the most current research and analysis on this field. It also provides a forum for supply-chain professionals by showcasing the best applied research. The latest business issues are explored in detail and succinctly in research papers.
Journal of Managing Value and Supply Chains
International Journal of Managing Value and Supply Chains, (IJMVSC), is an open access quarterly journal. It publishes articles about supply chain management and value. It is intended to be a platform for sharing innovative ideas and best practice in this area. Its content is diverse and includes articles on service and process management, as well articles about economics of value creation or extraction.
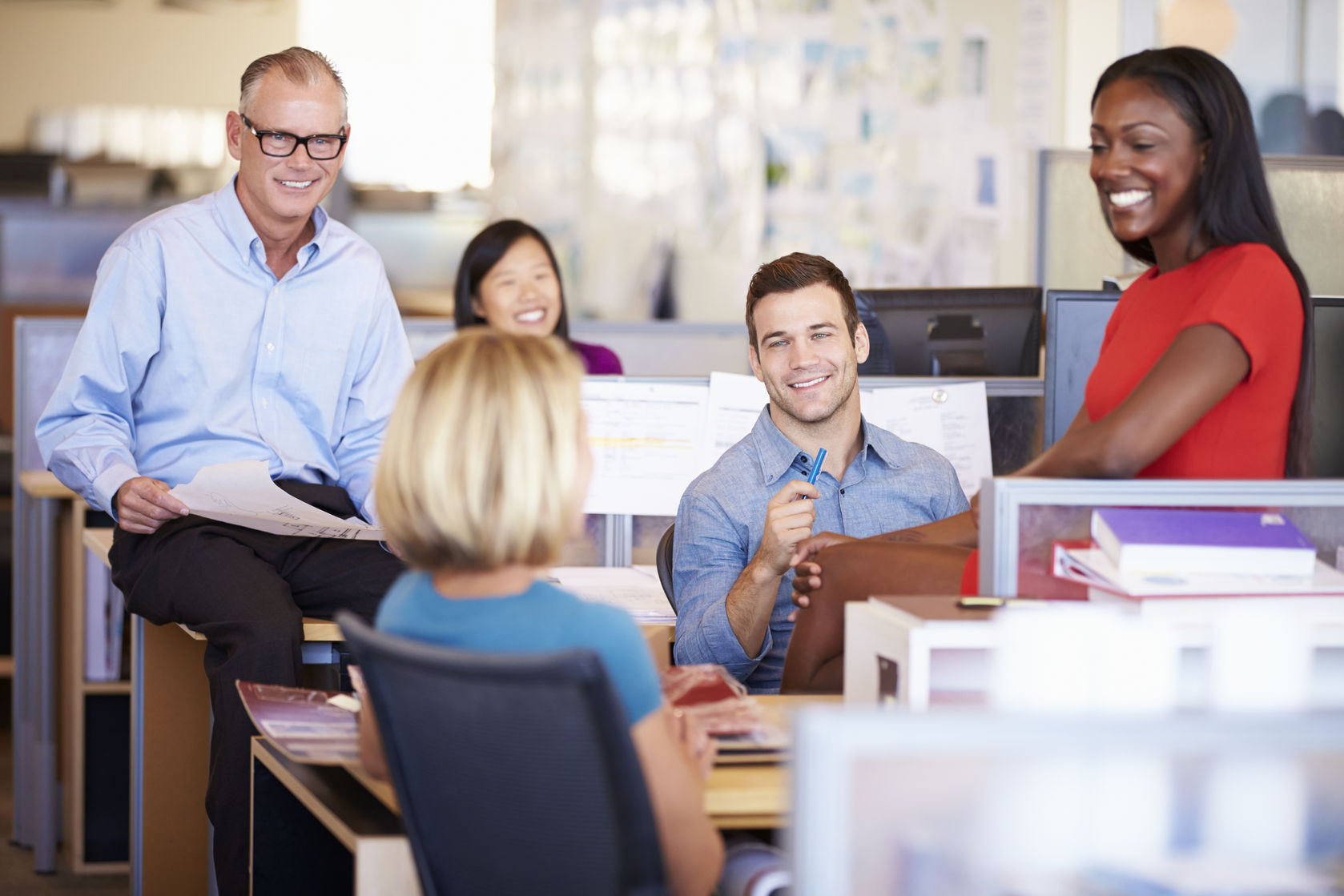
The journal accepts original papers, review articles and technical reports. Authors can also submit books reviews or notes related to their research topic. Submissions can either be invited or peer-reviewed.
Journal of Supply Chain Minded community
The Journal of Supply Chain Minded is an online resource for supply-chain professionals. This publication is a global resource because it focuses on the most recent trends in the industry. It features industry leaders and best practices in its articles. It's easy to understand and also incorporates social media.
The journal is an expanding online community that seeks to educate supply chain professionals. The journal aims to build new relationships between Supply Chain professionals through sharing their knowledge. There are also many online resources available to the journal.
Journal of Supply Chain Management Review
The Journal of Supply Chain Management Review (US) is a business management magazine that features articles on current trends in supply chain management. This quarterly magazine is a valuable resource for business professionals. Its purpose is to promote supply-chain management as an important part of business strategy. You'll also find articles by industry experts and practitioners.
The journal features articles by top supply chain management professionals and business school professors. This journal includes case studies that highlight the supply chain management practices of companies.
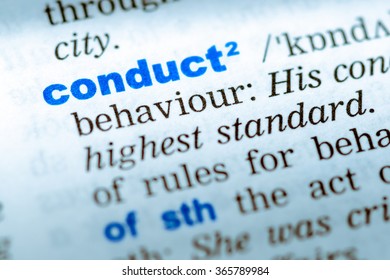
Journal of Supply Chain Management Review features
The Journal of Supply Chain Management Review publishes papers on recent advances in supply chain management. The articles cover topics such as the development of new supply networks and delivery methods, the challenges and opportunities presented by digital business environments and how Industry 4.0 will impact SMEs. The magazine also includes news and book reviews. It publishes bi-annually and has over 15 thousand subscribers.
This peer-reviewed journal publishes supply chain management papers and research papers. They provide practical guidance and cutting-edge information. The Journal features articles by professionals and business school students on current issues as well as case studies. The Journal features case study of companies that illustrate how their practices can improve supply-chain management.
FAQ
How does Six Sigma work
Six Sigma employs statistical analysis to identify problems, measure them and analyze root causes. Six Sigma also uses experience to correct problems.
The first step is to identify the problem.
The data is then analyzed and collected to identify trends.
Then, corrective actions can be taken to resolve the problem.
Finally, the data are reanalyzed in order to determine if it has been resolved.
This continues until the problem has been solved.
Why is it so hard to make smart business decisions?
Complex systems are often complex and have many moving parts. People who manage them have to balance multiple priorities while dealing with complexity and uncertainty.
The key to making good decisions is to understand how these factors affect the system as a whole.
You need to be clear about the roles and responsibilities of each system. You then need to consider how those individual pieces interact with each other.
Also, you should ask yourself if there have been any assumptions in your past behavior. If they don't, you may want to reconsider them.
For help, ask someone else if you're still stumped after all the above. They might see things differently than you and may have some insights that could help find a solution.
What are the five management steps?
The five stages of any business are planning, execution, monitoring, review, and evaluation.
Setting goals for the future is part of planning. Planning includes setting goals for the future.
Execution happens when you actually do the plan. Everyone involved must follow them.
Monitoring is the act of monitoring your progress towards achieving your targets. Regular reviews should be done of your performance against targets or budgets.
Reviews take place at the end of each year. They provide an opportunity to assess whether everything went well during the year. If not, it is possible to make improvements for next year.
Evaluation takes place after the annual review. It helps you identify the successes and failures. It also gives feedback on how well people did.
What are some of the common mistakes made by managers?
Managers sometimes make their own job harder than necessary.
They may not delegate enough responsibilities and not provide sufficient support.
Managers often lack the communication skills necessary to motivate and guide their teams.
Some managers set unrealistic expectations for their staff.
Managers may prefer to solve every problem for themselves than to delegate responsibility.
What is Six Sigma and how can it help you?
It's an approach to quality improvement that emphasizes customer service and continuous learning. This is an approach to quality improvement that uses statistical techniques to eliminate defects.
Motorola's 1986 efforts to improve manufacturing process efficiency led to the creation of Six Sigma.
It was quickly adopted by the industry and many companies are now using six-sigma to improve product design, production, delivery, customer service, and product design.
Statistics
- As of 2020, personal bankers or tellers make an average of $32,620 per year, according to the BLS. (wgu.edu)
- The average salary for financial advisors in 2021 is around $60,000 per year, with the top 10% of the profession making more than $111,000 per year. (wgu.edu)
- This field is expected to grow about 7% by 2028, a bit faster than the national average for job growth. (wgu.edu)
- UpCounsel accepts only the top 5 percent of lawyers on its site. (upcounsel.com)
- Your choice in Step 5 may very likely be the same or similar to the alternative you placed at the top of your list at the end of Step 4. (umassd.edu)
External Links
How To
How do you do the Kaizen method?
Kaizen means continuous improvement. Kaizen is a Japanese concept that encourages constant improvement by small incremental changes. It is a process where people come together to improve their processes.
Kaizen is one of Lean Manufacturing's most efficient methods. Kaizen is a concept where employees in charge of the production line are required to spot problems during the manufacturing process before they become major issues. This way, the quality of products increases, and the cost decreases.
Kaizen is a way to raise awareness about what's happening around you. Correct any errors immediately to avoid future problems. If someone is aware of a problem at work, he/she should inform his/her manager immediately.
Kaizen has a set of basic principles that we all follow. We always start from the end product and move toward the beginning. In order to improve our factory's production, we must first fix the machines producing the final product. First, we fix machines that produce components. Next, we fix machines that produce raw material. And finally, we fix the workers who work directly with those machines.
This is why it's called "kaizen" because it works step-by-step to improve everything. Once the factory is fixed, we return to the original site and work our way back until we get there.
Before you can implement kaizen into your business, it is necessary to learn how to measure its effectiveness. There are many ways you can determine if kaizen has been implemented well. One method is to inspect the finished products for defects. Another way to find out how productive your company has been since you implemented kaizen is to measure the increase in productivity.
A good way to determine whether kaizen has been implemented is to ask why. Was it just because it was the law or because you wanted to save money? Did you really think that it would help you achieve success?
If you answered yes to any one of these questions, congratulations! Now you're ready for kaizen.