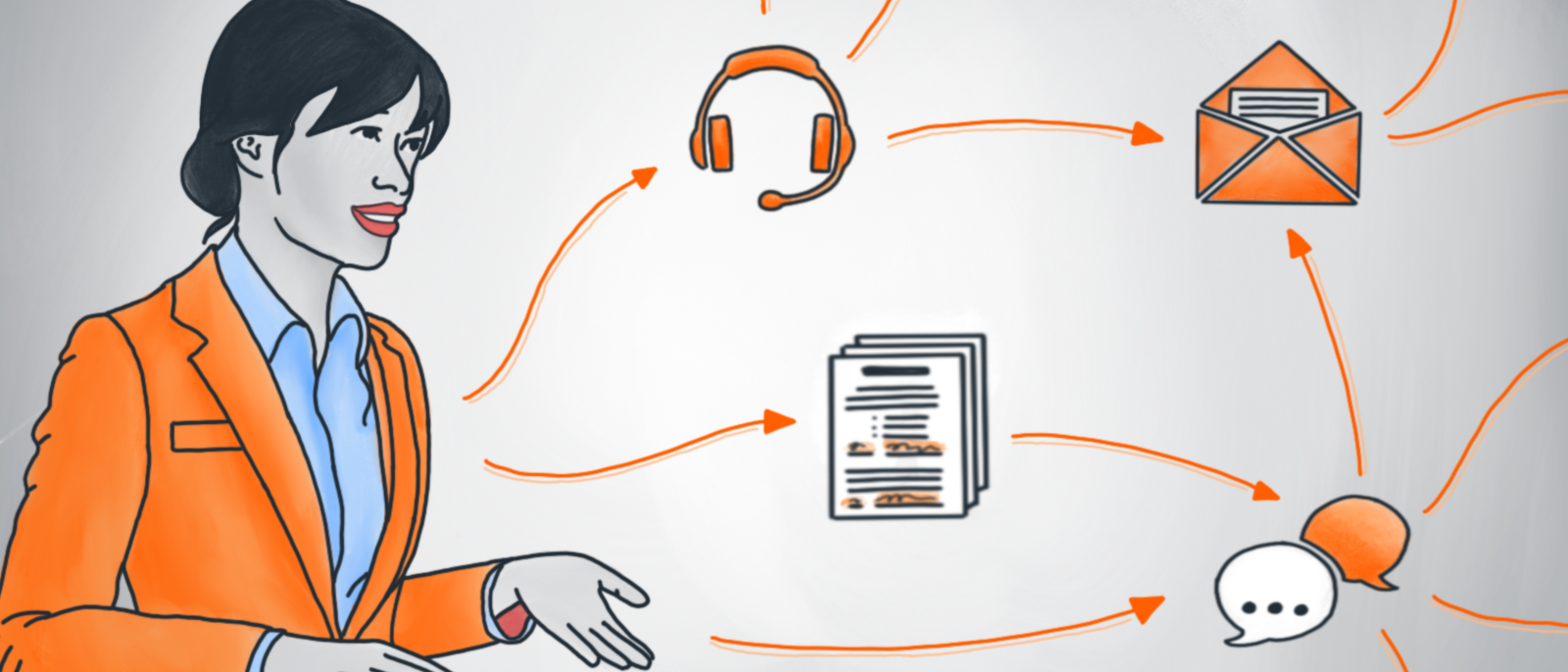
Resisting change is a common psychological response to change. This can be caused by fear, uncertainty, and lack of certainty. These obstacles can be overcome with a variety of strategies. These strategies can be used to reduce resistance to change and create an environment that encourages change.
Fear of unknown
Fear of unknown is a powerful emotion. Courage is required to overcome it. This emotion arises when we don't have enough information to make a decision. It can also manifests itself as intolerance for uncertainty. It can be managed by a number of strategies including creating a plan, practicing mindfulness, talking to a trusted family member, and making sure you have a backup plan. A healthy lifestyle can help you overcome fear of the unknown.
Fear of the Unknown is often accompanied in part by self-doubt. This makes you question your capabilities and gives you a sense of being out of control. It also inhibits your personal growth and hinders organisational progress. It can also lead you to procrastination.
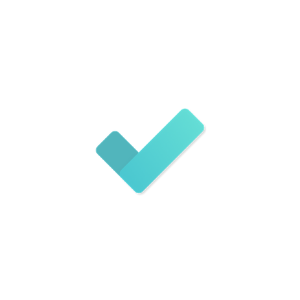
Incertitude
Uncertainty and fear are two of the top reasons people resist change. People tend to avoid the unknown because they fear the unknown. This can be overcome by creating certainty about the process and ensuring that it is well-planned. Leaders should provide as much information about the pending change and as much as possible acknowledge its impact.
Insecurity
Understanding the root causes behind resistance to change is the first step in overcoming insecurity. Insecurity affects everyone. People are often resistant to change because of a range of reasons.
Insecurity can be a natural response to changes and has many causes. Insecurity can lead to violent reactions for many people. People can feel scared or lose their job due to change. Even seemingly minor changes can be deeply troubling to individuals, such as automatic machinery and technological advances.
Controllability is not an option
Fear of change is the number one reason companies resist changes within their organizations. This fear is often caused due to mistrust and misunderstanding. People can feel threatened by being assigned a new manager to their team and may push back. Listening to employees can often be the best way of minimizing the effects.
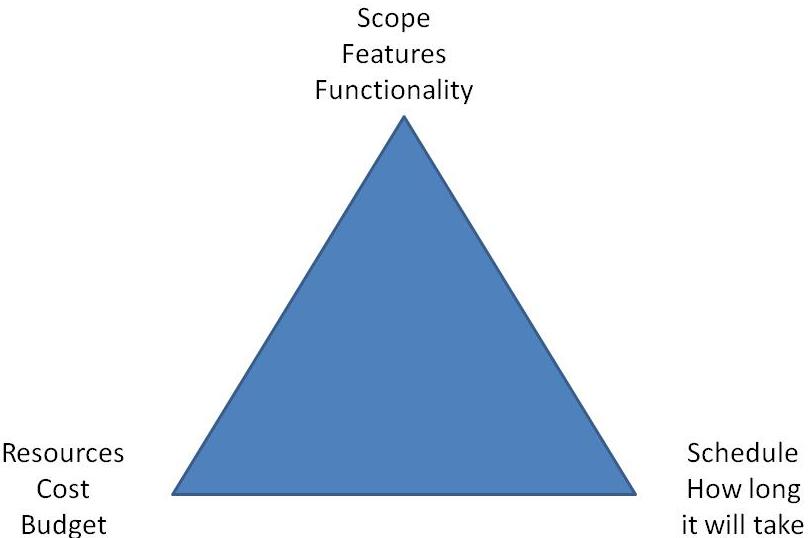
Lack of communication: Ineffective communication is another reason why people resist change. It is crucial for leaders to clearly communicate to employees the goals and changes that they are seeking. Failing to do this can cause disruption in efforts to implement the change.
FAQ
Why is it so important for companies that they use project management techniques
Project management techniques are used to ensure that projects run smoothly and meet deadlines.
This is due to the fact that most businesses rely heavily upon project work in order to produce goods, and services.
These projects are essential for companies.
Companies that do not manage their projects effectively risk losing time, money, or reputation.
What's the difference between a program and a project?
A program is permanent, whereas a project is temporary.
A project usually has a specific goal and deadline.
It is often done in a team that reports to another.
A program is usually defined by a set or goals.
It is usually implemented by a single person.
How can a manager improve his/her managerial skills?
By practicing good management skills at all times.
Managers must constantly monitor the performance of their subordinates.
It is important to take immediate action if your subordinate doesn't perform as expected.
It is important to be able identify areas that need improvement and what can be done to improve them.
Why is Six Sigma so popular?
Six Sigma is easy to use and can lead to significant improvements. It can also be used to help companies identify and focus on the most important aspects of their business.
How do you manage your employees effectively?
The key to effective management of employees is ensuring their happiness and productivity.
It also means having clear expectations of their behavior and keeping track of their performance.
To do this successfully, managers need to set clear goals for themselves and for their teams.
They must communicate clearly with their staff. They must communicate clearly with staff members.
They will also need to keep records about their team's activities. These include:
-
What was the result?
-
How much work was put in?
-
Who did it, anyway?
-
How did it get done?
-
Why?
This information is useful for monitoring performance and evaluating the results.
Statistics
- This field is expected to grow about 7% by 2028, a bit faster than the national average for job growth. (wgu.edu)
- Hire the top business lawyers and save up to 60% on legal fees (upcounsel.com)
- The profession is expected to grow 7% by 2028, a bit faster than the national average. (wgu.edu)
- As of 2020, personal bankers or tellers make an average of $32,620 per year, according to the BLS. (wgu.edu)
- Our program is 100% engineered for your success. (online.uc.edu)
External Links
How To
How does Lean Manufacturing work?
Lean Manufacturing techniques are used to reduce waste while increasing efficiency by using structured methods. They were developed in Japan by Toyota Motor Corporation (in the 1980s). It was designed to produce high-quality products at lower prices while maintaining their quality. Lean manufacturing focuses on eliminating unnecessary steps and activities from the production process. It includes five main elements: pull systems (continuous improvement), continuous improvement (just-in-time), kaizen (5S), and continuous change (continuous changes). Pull systems are able to produce exactly what the customer requires without extra work. Continuous improvement refers to continuously improving existing processes. Just-in–time refers when components or materials are delivered immediately to their intended destination. Kaizen stands for continuous improvement. Kaizen can be described as a process of making small improvements continuously. Finally, 5S stands for sort, set in order, shine, standardize, and sustain. These five elements can be combined to achieve the best possible results.
Lean Production System
The lean production system is based on six key concepts:
-
Flow - focuses on moving information and materials as close to customers as possible.
-
Value stream mapping- This allows you to break down each step of a process and create a flowchart detailing the entire process.
-
Five S's – Sort, Put In Order Shine, Standardize and Sustain
-
Kanban is a visual system that uses visual cues like stickers, colored tape or stickers to keep track and monitor inventory.
-
Theory of constraints - identify bottlenecks in the process and eliminate them using lean tools like kanban boards;
-
Just-in time - Get components and materials delivered right at the point of usage;
-
Continuous improvement - incremental improvements are made to the process, not a complete overhaul.