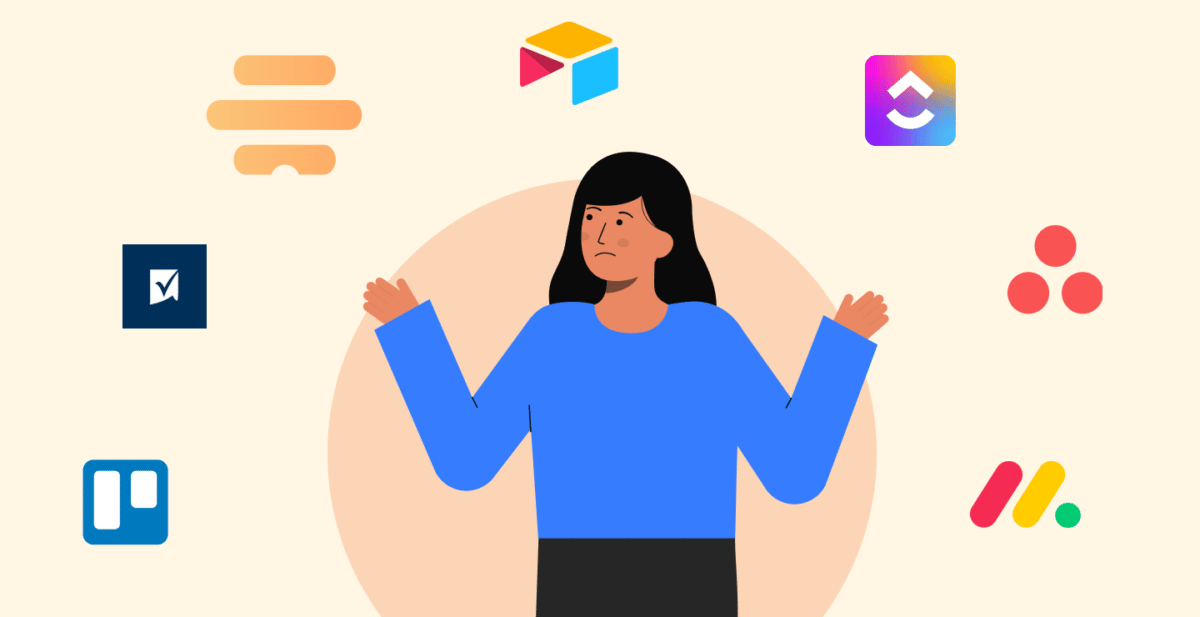
Supply chain management refers to the management of goods from raw materials to the final product. The supply chain involves many interdependent processes, which can pose risks. These include changes in workforce and business operations, climate and environment, social and demographic shifts, and changing climate and environment. Supply chain management is essential to any business's success.
Management of the flow goods from raw materials to final product
Supply chain management involves coordinating the flow of goods between raw materials and finished products. It helps companies manage their inventory and improve the quality of their products. It can also be a way to increase revenue. Companies can have a competitive advantage by taking a holistic view of supply chain management.
Plan
During the planning phase, supply chain managers analyze the various factors that can affect the supply chain. These factors include the availability and pricing of raw materials as well as the distribution channels. It is vital that the supply chains are prepared for every possible scenario and that all variables align to meet customer needs. A well-planned and planned supply chain can help to reduce costs by eliminating wasteful production and overproduction. Additionally, it can assist companies in coping with limited supply situations.
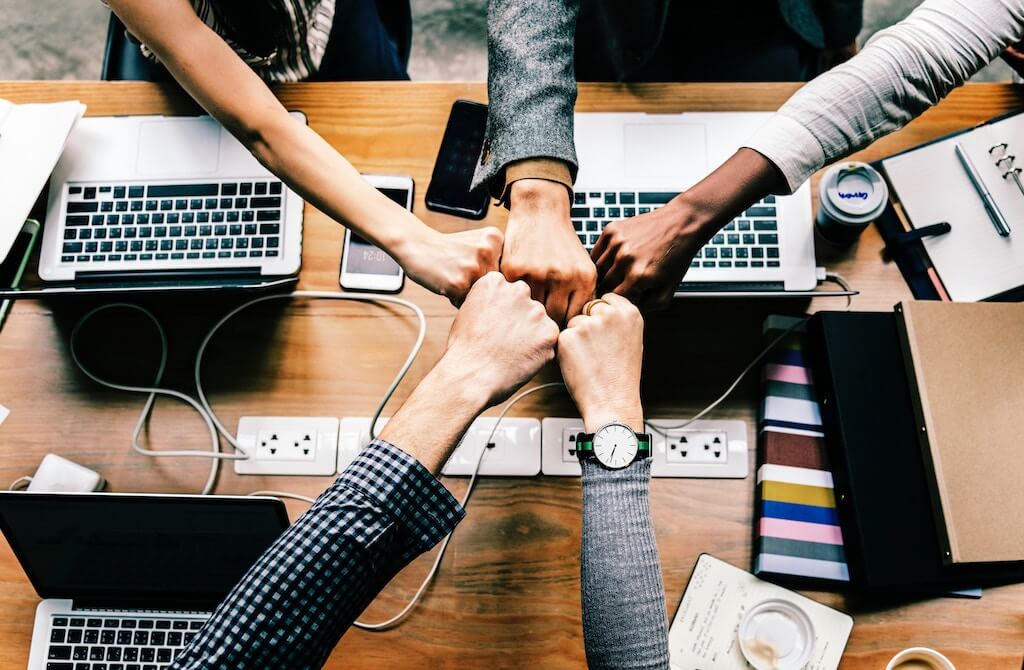
Sourcing
Supply chain management (SCM), is the whole process of delivering products from the raw material to their final destination. This includes production planning, demand forecasting, and logistics. This all affects customer satisfaction and company profitability.
Manufacturing
Management of manufacturing supply chain is concerned with controlling the flow and movement of goods and services into and out of a company. This model allows a business to increase production and efficiency, while also lowering labor and material costs. Optimal supply chain management also ensures that a business's infrastructure is planned in a manner that is in the best interest of the company.
Delivery
Supply chain management includes delivery. It involves receiving and storing products as well retrieving them and preparing them for dispatch. This process is crucial to the viability and success of delivery. Proper planning and information exchange between departments can increase delivery performance and reduce logistical costs.
Returns
This is a management strategy that minimizes unwanted product flow. This process can be applied to improve operational efficiencies. This involves many sub-processes. These activities are also interdependent with other supply chain management processes.
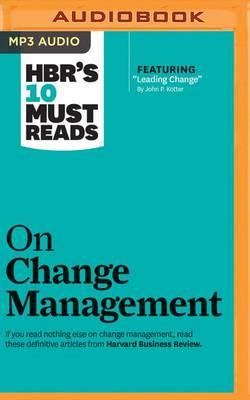
Controlling costs
Supply chain management must include cost control. It ensures that all costs in a supply chain remain within budget. It also helps determine how to allocate costs across the supply chain. Cost analysis can help increase competitiveness by helping to determine how costs should be allocated.
FAQ
What is Kaizen, exactly?
Kaizen is a Japanese term which means "continuous improvement." This philosophy encourages employees to continually look for ways to improve the work environment.
Kaizen is based upon the belief that each person should be capable of doing his or her job well.
What are the main management skills?
Management skills are essential for any business owner, whether they're running a small local store or an international corporation. These include the ability and willingness to manage people, finances as well resources, time and space.
When you need to manage people, set goals, lead teams, motivate them, solve problems, develop policies and procedures and manage change, management skills are essential.
You can see that there are many managerial duties.
Why is project management important for companies?
Project management techniques are used in order to ensure projects run smoothly, and that deadlines are met.
This is because most businesses rely on project work for their products and services.
These projects require companies to be efficient and effective managers.
Companies that do not manage their projects effectively risk losing time, money, or reputation.
Statistics
- As of 2020, personal bankers or tellers make an average of $32,620 per year, according to the BLS. (wgu.edu)
- The profession is expected to grow 7% by 2028, a bit faster than the national average. (wgu.edu)
- 100% of the courses are offered online, and no campus visits are required — a big time-saver for you. (online.uc.edu)
- This field is expected to grow about 7% by 2028, a bit faster than the national average for job growth. (wgu.edu)
- Our program is 100% engineered for your success. (online.uc.edu)
External Links
How To
What is Lean Manufacturing?
Lean Manufacturing uses structured methods to reduce waste, increase efficiency and reduce waste. They were created in Japan by Toyota Motor Corporation during the 1980s. It was designed to produce high-quality products at lower prices while maintaining their quality. Lean manufacturing emphasizes removing unnecessary steps from the production process. It includes five main elements: pull systems (continuous improvement), continuous improvement (just-in-time), kaizen (5S), and continuous change (continuous changes). It is a system that produces only the product the customer requests without additional work. Continuous improvement means continuously improving on existing processes. Just-in-time is when components and other materials are delivered at their destination in a timely manner. Kaizen means continuous improvement, which is achieved by implementing small changes continuously. Fifth, the 5S stand for sort, set up in order to shine, standardize, maintain, and standardize. These five elements work together to produce the best results.
Lean Production System
Six key concepts underlie the lean production system.
-
Flow is about moving material and information as near as customers can.
-
Value stream mapping - break down each stage of a process into discrete tasks and create a flowchart of the entire process;
-
Five S's: Sort, Shine Standardize, Sustain, Set In Order, Shine and Shine
-
Kanban: Use visual signals such stickers, colored tape, or any other visual cues, to keep track your inventory.
-
Theory of constraints - identify bottlenecks in the process and eliminate them using lean tools like kanban boards;
-
Just-in-time delivery - Deliver components and materials right to your point of use.
-
Continuous improvement - make incremental improvements to the process rather than overhauling it all at once.