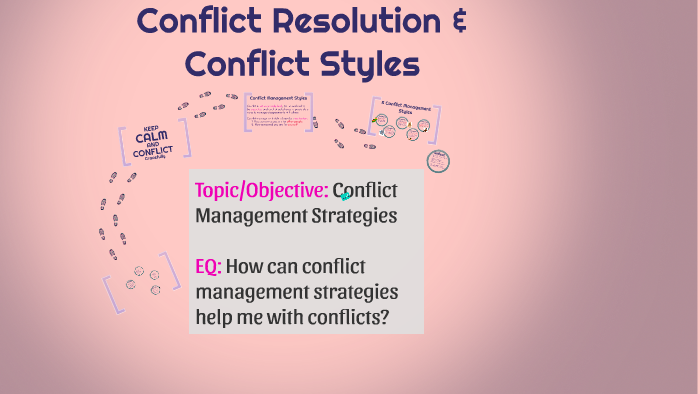
Behaviour based safety (BBS), is a way to improve safety. It applies the science behind behaviour change to real-world safety problems. This creates safety partnerships between management and employees by focusing attention on everyday safety behavior. It is designed to make the workplace safer.
Safety Based on Behaviour
Behaviour-Based Safety (BBS) is a process that encourages workplaces to change their behaviour to increase safety. This process includes collecting safety behavior data, redesigning work procedures, and introducing safer work practices. The system is then evaluated to make sure it works. Behaviour Based safety is a dynamic process. It changes as new information becomes available. In other words, the original model may not work after only a few weeks. BBS programs can be complex, so it is important to consider a change management process and training.
A great safety program should be inclusive of a variety topics and activities. It should encourage employees to take responsibility for their own safety. Many times, employees' actions can lead to injuries and incidents. High and low risk behavior should be addressed in a safety program.
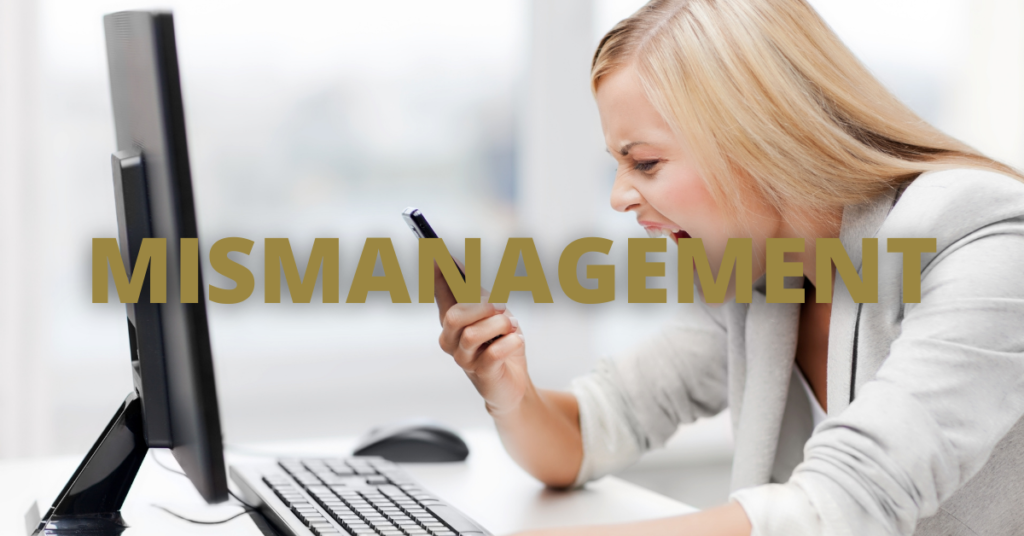
Behaviour-Based Safety Culture
Using a behaviour-based safety culture to improve safety performance can improve a number of important metrics. It can lower accident rates and also reduce the possibility of future incidents. Reluctant to change makes it difficult to implement such an approach. However, investing in a "Behaviour-Based Safety culture" will ensure that people react in the correct way at critical moments. This can result in long-term economic benefits.
In addition to training employees about how to act safely in the workplace, behaviour-based safety cultures should also include a clear set of policies. These policies should be a comprehensive overview of the company's safety policy and should also include mechanisms for continual improvement. These policies should also contain regular safety training for all employees.
Safety system based on behaviour
A Behaviour-based safety system of measure is a way to measure safety performance in the workplace. This system of measurement helps identify the key workplace behaviours. It then designs an effective prevention or control program. It can also help to make a business case for solutions to prevent workplace injuries or accidents.
Behavioral safety observations are usually conducted daily, weekly, or monthly. They should be able to record both dangerous and positive behavior and make suggestions for improvement.
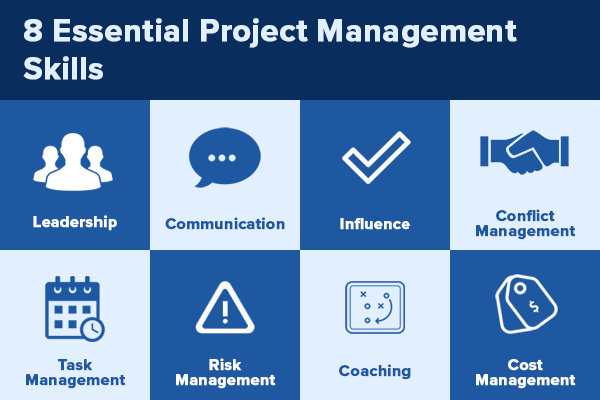
Benefits of a BBS-Program
BBS can improve safety culture within your company. Employees can use this program to hold their colleagues accountable for unsafe behaviors. BBS can help prevent accidents as well as improve your employees' overall health. It can help prevent diseases and injuries from exposure to hazardous chemicals.
To make the program effective, you need to set measurable goals. Goals can include the number of near-miss incidents that occur per year or the percentage of employees who wear proper PPE. It is important to set attainable but also sustainable goals, as employees will be discouraged if they are not met. Also, you should have a clear plan to implement the program.
FAQ
Why is it so hard to make smart business decisions?
Complex systems with many moving parts are the hallmark of businesses. People who manage them have to balance multiple priorities while dealing with complexity and uncertainty.
To make good decisions, you must understand how these factors affect the entire system.
This requires you to think about the purpose and function of each component. You then need to consider how those individual pieces interact with each other.
Also, you should ask yourself if there have been any assumptions in your past behavior. You might consider revisiting them if they are not.
You can always ask someone for help if you still have questions after all of this. They might see things differently than you and may have some insights that could help find a solution.
What is Kaizen?
Kaizen is a Japanese term which means "continuous improvement." This philosophy encourages employees to continually look for ways to improve the work environment.
Kaizen is a belief that everyone should have the ability to do their job well.
How does a manager motivate his/her employees?
Motivation is the desire for success.
Engaging in something fun can be a great way to get motivated.
You can also get motivated by seeing your contribution to the success or the improvement of the organization.
If you are a doctor and want to be one, it will likely be more rewarding to see patients than to read medical books every day.
The inner motivation is another type.
You may feel strongly that you are responsible to help others.
You might even enjoy the work.
Ask yourself why you aren't feeling motivated.
You can then think of ways to improve your motivation.
What is the meaning of "project management?"
That is the management of all activities associated with a project.
This includes defining the scope, identifying the requirements and preparing the budget. We also organize the project team, schedule the work, monitor progress, evaluate results, and close the project.
What is the difference between Six Sigma Six Sigma and TQM?
The main difference in these two quality management tools lies in the fact that six sigma is focused on eliminating defects and total quality management (TQM), emphasizes improving processes and reducing costs.
Six Sigma can be described as a strategy for continuous improvement. It emphasizes the elimination or minimization of defects through statistical methods such control charts and p charts.
The goal of this method is to reduce variation in product output. This is done by identifying and correcting the root causes of problems.
Total Quality Management involves monitoring and measuring every aspect of the organization. This includes training employees to improve their performance.
It is frequently used as an approach to increasing productivity.
What are some common mistakes managers make?
Sometimes managers make their job harder than they need to.
They may not delegate enough responsibilities to staff and fail to give them adequate support.
Many managers lack the communication skills to motivate and lead their employees.
Some managers set unrealistic expectations for their staff.
Managers may prefer to solve every problem for themselves than to delegate responsibility.
How can a manager enhance his/her leadership skills?
You can improve your management skills by practicing them at all times.
Managers need to monitor their subordinates' performance.
If you notice your subordinate isn't performing up to par, you must take action quickly.
You should be able pinpoint what needs to improve and how to fix it.
Statistics
- This field is expected to grow about 7% by 2028, a bit faster than the national average for job growth. (wgu.edu)
- 100% of the courses are offered online, and no campus visits are required — a big time-saver for you. (online.uc.edu)
- UpCounsel accepts only the top 5 percent of lawyers on its site. (upcounsel.com)
- Our program is 100% engineered for your success. (online.uc.edu)
- As of 2020, personal bankers or tellers make an average of $32,620 per year, according to the BLS. (wgu.edu)
External Links
How To
How do I get my Six Sigma certification?
Six Sigma is a tool for quality management to improve processes and increase efficiency. Six Sigma is a method that helps companies get consistent results from their operations. The name comes from the first two letters of the Greek word "sigmas" which mean "six." Motorola was the first to develop this process. Motorola realized that it was important to standardize manufacturing processes so they could produce products quicker and cheaper. Because of the number of people involved in the work, they had problems maintaining consistency. To overcome this problem they turned to statistical tools such control charts and Pareto analyses. They would then apply these techniques to all aspects of their operation. This would allow them to make any necessary changes. To get Six Sigma certified, there are three key steps. First, you need to determine if your qualifications are valid. Before you take any exams, you'll need to take some classes. Once you pass those classes, the test will begin. You will want to remember everything you learned in the class. After that, you can take the test. If you pass, you'll get certified. Finally, you can add your certifications on to your resume.