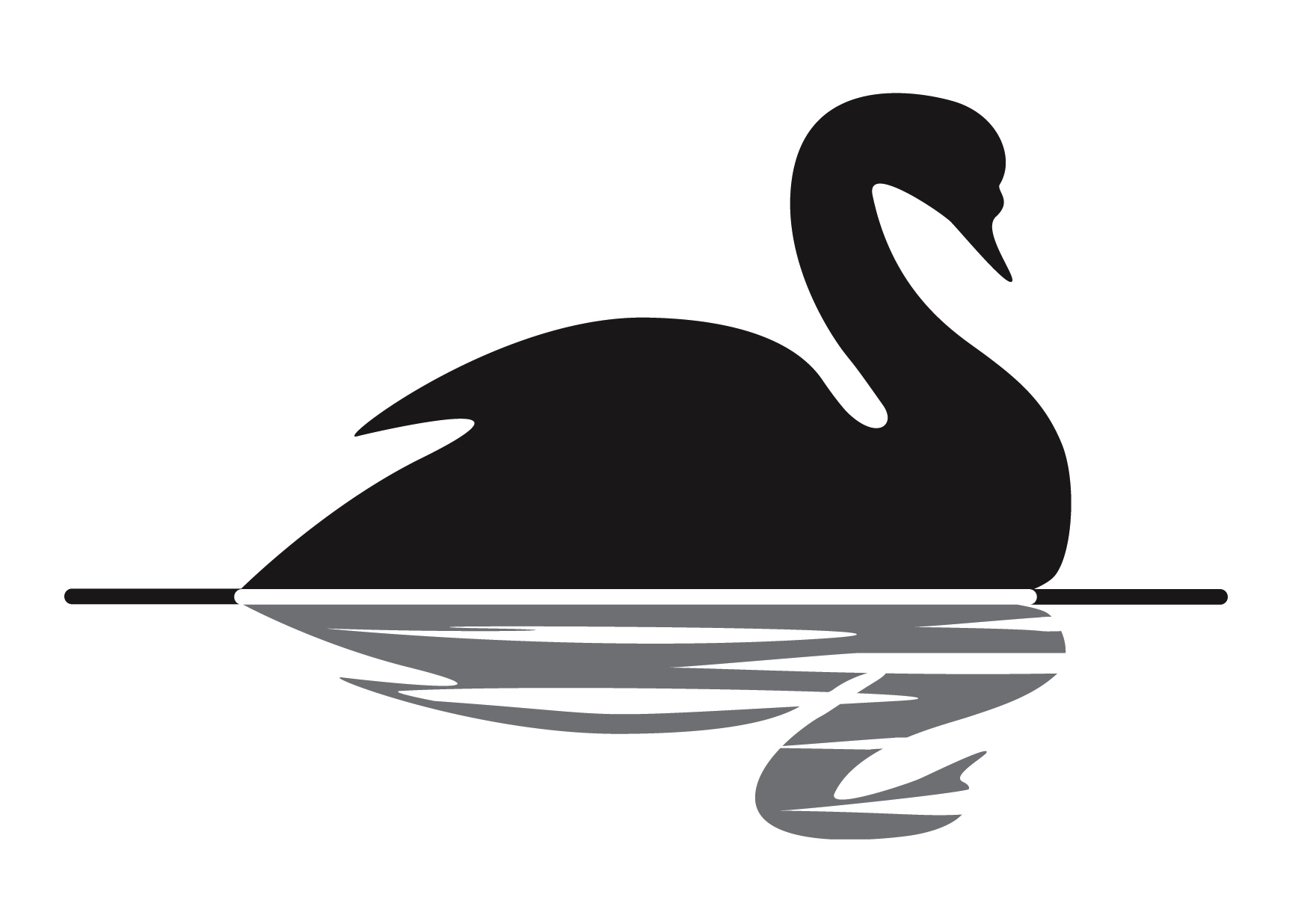
For companies who need to fulfill ongoing customer requirements, the demand management supply chains is crucial. It is essential to understand how demand works and devise a strategy to address them. Demand management includes both forecasting as well as adaptability. This will allow a company to satisfy customer needs and maximize profit.
Factors that influence demand in the demand management supply chains
Demand management is critical to your business, no matter if you're a service provider or a product manufacturer. This strategy will allow you to optimize your supply chain and maximize profitability. Demand management can help you increase your organizational agility and competitive advantage. It also increases your product availability and your response time to changes of demand. It can also help you introduce new products and services smoothly and efficiently.
Understanding how to balance both supply and demand is key to successful demand management. You can plan inventory better, lower costs, and increase customer satisfaction by properly managing demand. You can also improve forecasting, and prevent over-stocking. Demand management is designed to improve sales growth and profit margins.
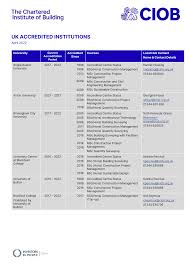
POS data is a crucial data source
POS data is a valuable tool to improve the supply and demand management processes. It provides data about customer inventory levels and order variability, as well the sell-through rate, fill rate, sold-through rate, and sell rate. Businesses can make better decisions based on this information. In addition, it enables better communication among various levels.
Demand planning software can generate detailed forecasts from POS data. The data can also be broken down into SKUs as well locations and dates. It can also be used to detect stockouts or localized sales trends. It can be complicated for new users to work with POS-related data. Different retail partners might provide data in different formats or use different data transfer methods. Moreover, partners might not have the ability to share their POS information.
Forecasting is a crucial part of demand management supply chains
Forecasting is essential for demand management supply chain planning. Companies can use accurate forecasts to help determine the inventory required to meet customer needs. They can also help improve logistics and distribution planning. Companies can avoid stock-outs and the "Bullwhip Effect" by anticipating demand and understanding its impact.
Most forecasts are based on software or mathematical methods. They are updated frequently and should account for all the various intermediates, finished goods, and raw materials involved in a supply chain. Additionally, forecasts should take into account both dependent and independent demand.
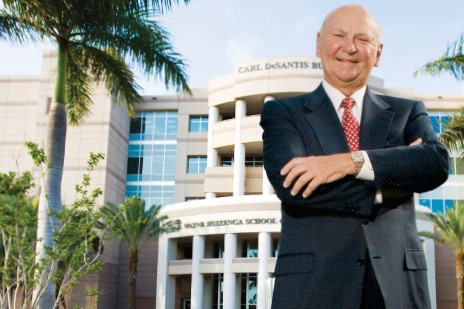
Adaptability is a key factor in demand management supply chain
Companies must be flexible and adaptable in an ever-changing business environment. An adaptive supply network architecture can increase the resilience of supply chains and enhance competitive advantage. However, to be effective, it must consider all aspects of the supply chain, not just the demands of the end customer.
Companies that are flexible create flexible organizational structures, decentralize decision-making and have adaptability. This approach fosters trust and fluidity among the participants. Toyota has created several adaptive systems, such as the automotive supply chains. EBay, which relies on online payment systems and seller ratings, is another example.
FAQ
What is the main difference between Six Sigma Six Sigma TQM and Six Sigma Six Sigma?
The key difference between the two quality management tools is that while six-sigma focuses its efforts on eliminating defects, total quality management (TQM), focuses more on improving processes and reducing cost.
Six Sigma stands for continuous improvement. It emphasizes the elimination of defects by using statistical methods such as control charts, p-charts, and Pareto analysis.
This method has the goal to reduce variation of product output. This is done by identifying root causes and rectifying them.
Total quality management involves measuring and monitoring all aspects of the organization. It also includes training employees to improve performance.
It is often used as a strategy to increase productivity.
What are the steps that management takes to reach a decision?
Managers face complex and multifaceted decision-making challenges. It involves many factors, including but not limited to analysis, strategy, planning, implementation, measurement, evaluation, feedback, etc.
Remember that people are humans just like you, and will make mistakes. This is the key to managing them. As such, there are always opportunities for improvement, especially when you put in the effort to improve yourself.
In this video, we explain what the decision-making process looks like in Management. We will discuss the various types of decisions, and why they are so important. Every manager should be able to make them. The following topics will be covered.
Why is project management so important?
Project management techniques are used to ensure that projects run smoothly and meet deadlines.
Because most businesses depend heavily on project work to produce goods or services,
Companies need to manage these projects efficiently and effectively.
Companies can lose time, money, and reputation if they don't have a good project management system.
What is Six Sigma?
It is a way to improve quality that places emphasis on customer service and continuous learning. The goal is to eradicate defects through statistical techniques.
Motorola developed Six Sigma in 1986 to help improve its manufacturing processes.
This idea quickly spread throughout the industry. Today, many organizations use six sigma methods for product design, production and delivery.
Statistics
- UpCounsel accepts only the top 5 percent of lawyers on its site. (upcounsel.com)
- Your choice in Step 5 may very likely be the same or similar to the alternative you placed at the top of your list at the end of Step 4. (umassd.edu)
- The profession is expected to grow 7% by 2028, a bit faster than the national average. (wgu.edu)
- The BLS says that financial services jobs like banking are expected to grow 4% by 2030, about as fast as the national average. (wgu.edu)
- As of 2020, personal bankers or tellers make an average of $32,620 per year, according to the BLS. (wgu.edu)
External Links
How To
How can I obtain my Six Sigma license
Six Sigma is a quality management tool to improve processes and increase efficiency. It is a process that helps businesses achieve consistent results in their operations. The name comes from the first two letters of the Greek word "sigmas" which mean "six." Motorola created this process in 1986. Motorola recognized that they had to standardize their manufacturing processes to produce faster and more affordable products. There were many people doing the work and they had difficulty achieving consistency. To solve this problem, they decided to use statistical tools such as control charts and Pareto analysis. They would then apply these techniques to all aspects of their operation. After applying the technique, they could make improvements wherever there was potential. When you are trying to obtain your Six Sigma certification, there are three steps. The first step is to find out if you're qualified. Before you take any exams, you'll need to take some classes. After passing the classes, you will be able to take the tests. It is important to review everything that you have learned in class. After that, you can take the test. You will be certified if you pass the test. Final, your certifications can be added to you resume.